3D Scanning & Data Capture Costs and Platforms
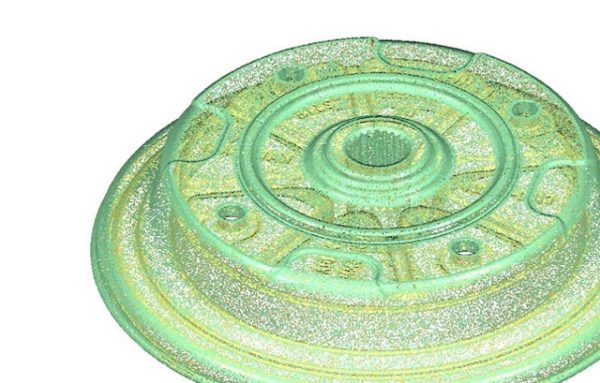
3D Scanning & Data Capture Costs and Platforms
In a continuation of our discussion in our previous blog post, today, we look at the costs associated with 3D scanning and the platforms used in 3D scanning.
3D scanning enhances the design process, speeds up and reduces data collection errors, saves time and is an attractive alternative to traditional data collection techniques. 3D scanning is also used for mobile mapping, surveying, scanning of buildings and building interiors, and in archaeology.
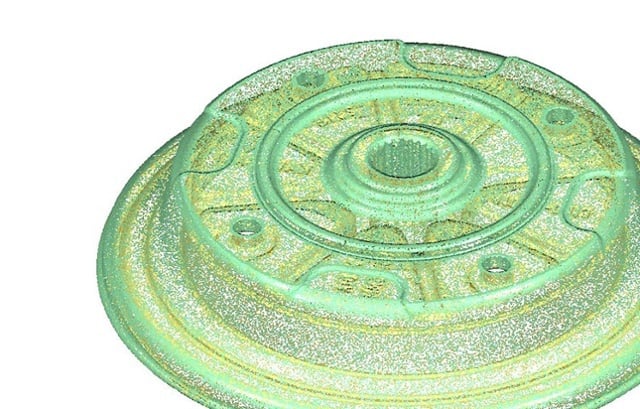
For enhanced laser scanning applications and/or high material throughput during production, scanning systems with more than one scan head are used. Here the software has to control what is done exactly within such a multihead application: it is possible that all available heads have to mark the same to finish processing faster or that the heads mark one single job in parallel where every scanhead performs a part of the job in case of large working areas.
Costs
3D scanning systems can run from very low cost to extremely high cost. In general, low-cost 3D scanners are for use by hobbyists and do not always give the most accurate results, such as would be needed in aerospace, for instance. The higher the accuracy, the higher the costs.
However, you want your budget to stretch as far as it can – of course, without sacrificing performance or quality. That is the ideal. In the area of laser scanning and inspection, one cost-cutting measure is to settle for a lower-accuracy system. Lower standards are cheap. For precision manufacturers who are interested in quality, that’s not a viable option. Here are 4 ideas focused on controlling scanning and modeling costs while maintaining accuracy and integrity of the results.
- Limit the number of parts to be scanned.
Designers often want to see variability between parts to determine tolerances for a new product. Tolerances should be developed for the part assembly, performance metrics, and industry standards. Variation from part to part only gives a tiny snapshot of how the manufacturing process performed when the parts were being made. Scan multiple parts when you need averages to produce a “golden model” of the point cloud, or if you want “good” and “bad” results compared, or if you need another valid comparison such as between cavities or between suppliers.
- Scan only one side.
If only one area of the part is critical to you, don’t spend the money to scan all features. Much more time is involved in producing a 360-degree scan of an object. Scanning a single side is most useful if you have a critical sealing surface or the part is uniform in thickness (such as a precision metal stamping).
- Use the “least” level of file output that will work for your application.
This advice comes with a word of caution; don’t compromise by purchasing a file you can’t use. With that in mind, the cost of the project increases along a progression of file types, generally in this order: point cloud, STL, comparative analysis, NURBS surface, native parametric, 2D prints. The farther down the line, the more cost that’s involved. Choose the file type that best fits your application.
- Outsource your scanning
Rather than purchasing a laser scanner and training the personnel to perform the scans, your least expensive solution may simply be to outsource the job. By hiring a CAD Perfect® service, you can be assured of excellent quality work from start to finish. This is particularly true if your parts are stationary or too large to handle.
CAD Perfect® scanning services can scan nearly anything — from the face of a penny to the contours of a fighter jet and everything in between. A variety of scanning technologies are leveraged as needed given constraints of material, size, and complexity. CAD Perfect® Scanning Platforms include; (1) Red Light Laser, (2) Blue Light Laser, (3) White Light, (4) CMM-Mounted Systems. (5) Arm-Mounted Portable Systems.
Recent Posts
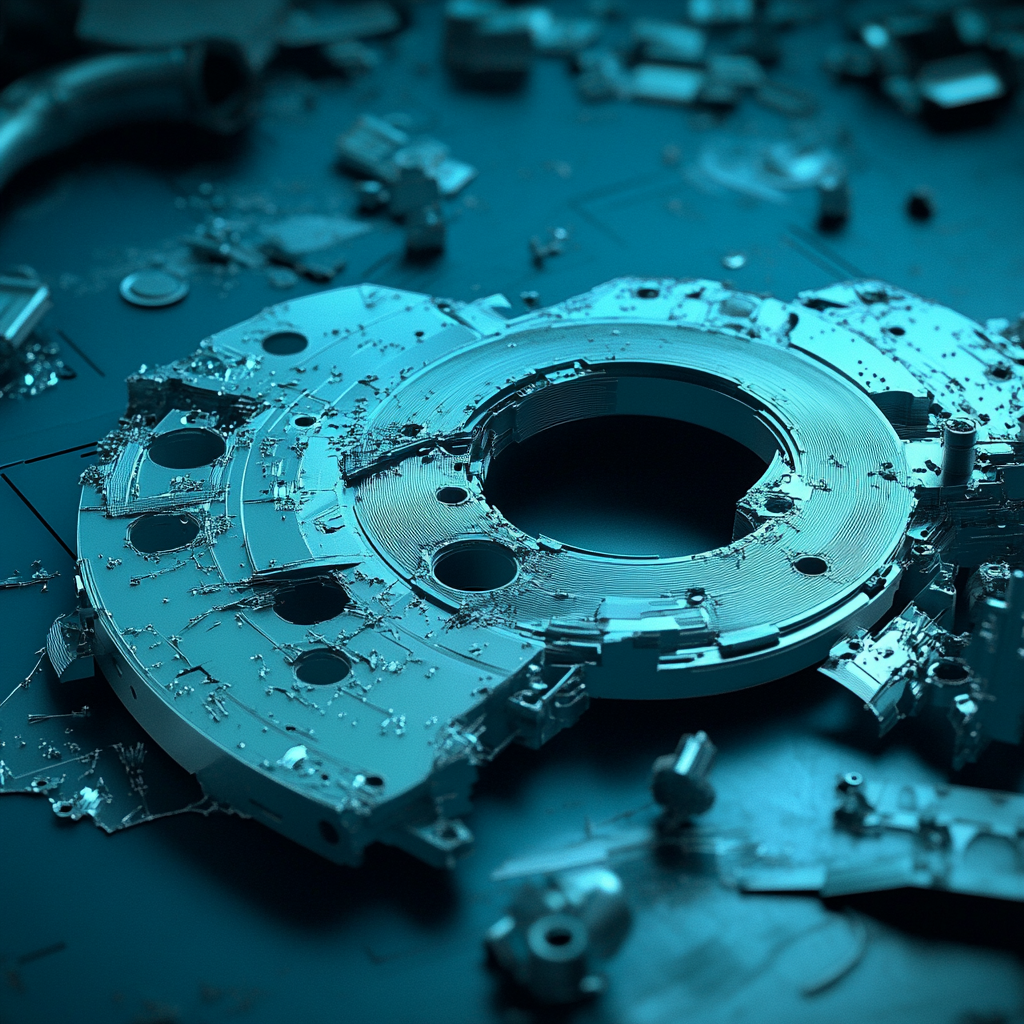
5 Common CAD Mistakes and How to Avoid Them
We came up with 5 common issues that we see, and our expert advice when it comes to avoiding these issues.
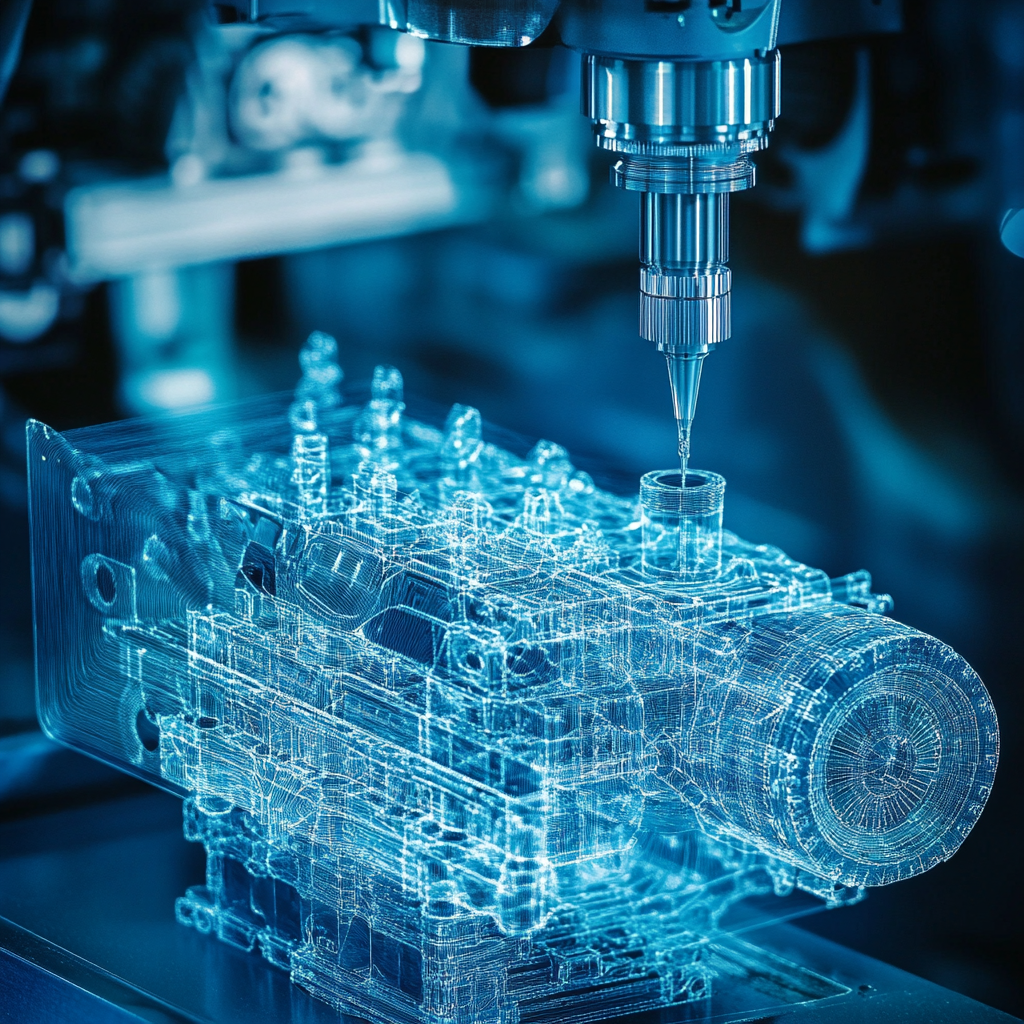
Techniques to Save Money on Manufacturing Your 3D CAD Model
Our team of outsourced CAD experts wants to talk about ways that your engineering team can save money on manufacturing with each 3D CAD model in 2024.
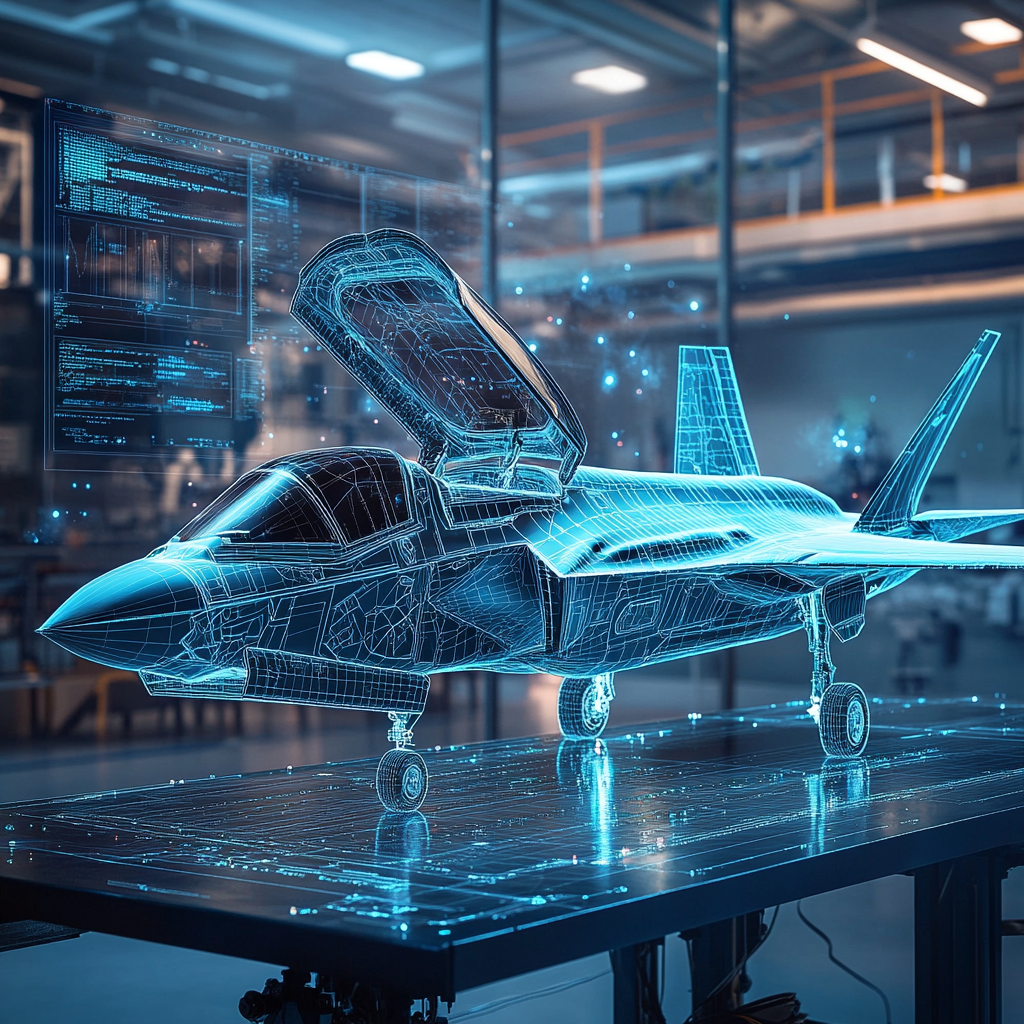
Shortcuts to Save Time on CAD Conversions
a quick tip to save money on each of your CAD conversions