All About Surface Modeling and Solid Modeling
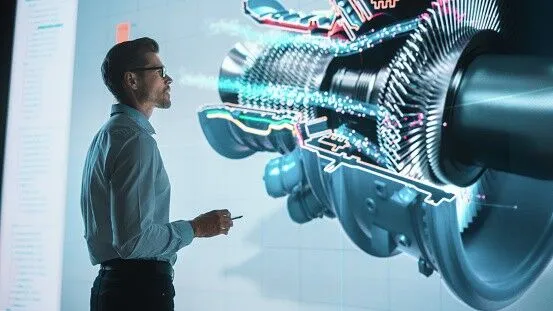
There is a lot of confusion surrounding surface modeling and how it compares to solid modeling. In this quick guide, we’ll explain the differences and teach you everything you need to know. This is valuable information for any engineer.
What Is Surface Modeling?
Surface modeling is a form of modeling that’s used in 3D CAD programs. It’s the product of defining each surface of a part, then combining them until you have the 3D part.
In reality, the end result looks identical whether you use surface modeling or solid modeling, the approach is just slightly different between the two.
People typically refer to parts made in SolidWorks (or similar) as “solid modeling”, and parts made in Alias (or similar) as “surface modeling”. In surface modeling, the process can be much more complicated and convoluted.
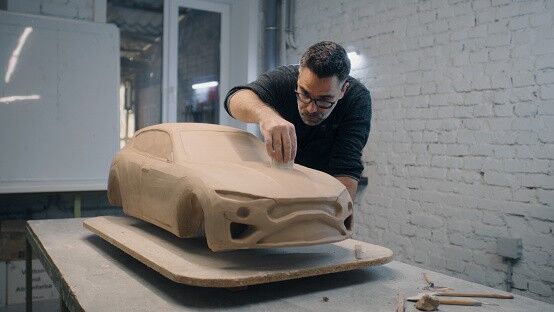
A Quick Example of Surface vs Solid Modeling
To better describe the process, let’s give a quick example. Imagine you want to design a solid model of a car — in fact, the car industry is where surface modeling is incredibly popular.
If you were a solid modeling engineer, you would sketch a side view and extrude it out. Then you’d sketch a top view, extrude that down, and then deal with the front view (or some variation of this process). Each step is a sketch, then an addition or subtraction to the model.
In surface modeling, you would draw all six faces of the car, then stitch the six drawings together to create a stitched part. If you do it correctly, then you can also add a volume to the sketches and create a solid part.
The end result could be identical between the two, it’s just the process that’s very different.
Another thing to mention is that both of these files will be different in the feature tree. If you wanted to go back and change the part, then your approach would be different.
This is the big reason why our clients might ask us to model something as surfaces or a solid in the first place — you should get a part that you’re comfortable working with. If you only work in solid modeling and you receive a surface-modeled part, then you’re going to face a huge uphill battle as you struggle through the learning curve.
Which Is Better, Surface Modeling or Solid Modeling?
At CAD/CAM Services, our team has made millions of models over our decades in business. That means that we can speak on this difference with a good level of confidence.
So, is surface modeling or solid modeling the better option? The real answer is that it truly doesn’t matter. The better option is whichever one you have more experience with. Again, if your team only knows how to do solid modeling, there’s no point in asking for any other files besides solid-modeled files.
When both options are done correctly, the final result looks and acts the same. The difference is whenever you need to change the model or add anything.
Conclusion
We just quickly covered the difference between surface modeling and solid modeling. If you want to learn more or you want a model of your own, reach out to our experts at CAD/CAM Services. We have been creating 3D models for customers for the past 30 years, and we would love to help you. Get a free quote today.
Recent Posts
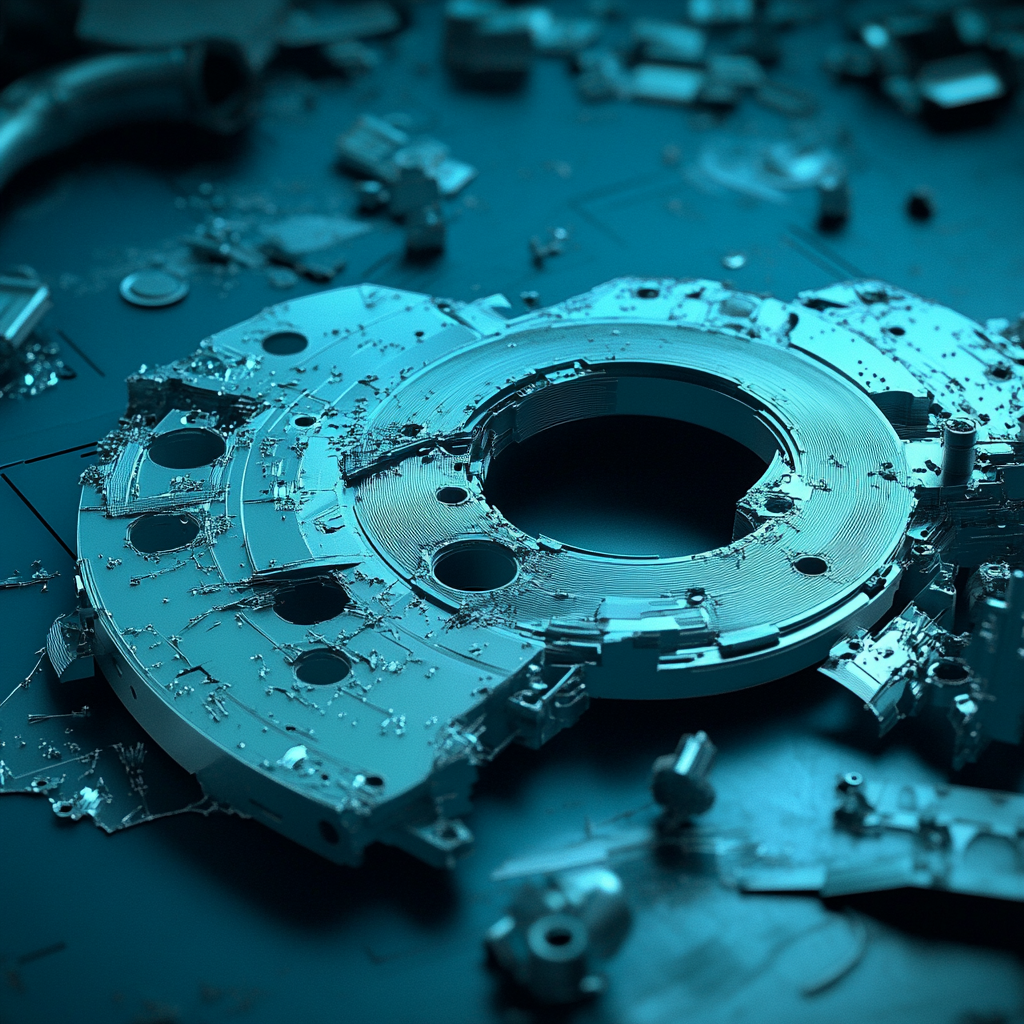
5 Common CAD Mistakes and How to Avoid Them
We came up with 5 common issues that we see, and our expert advice when it comes to avoiding these issues.
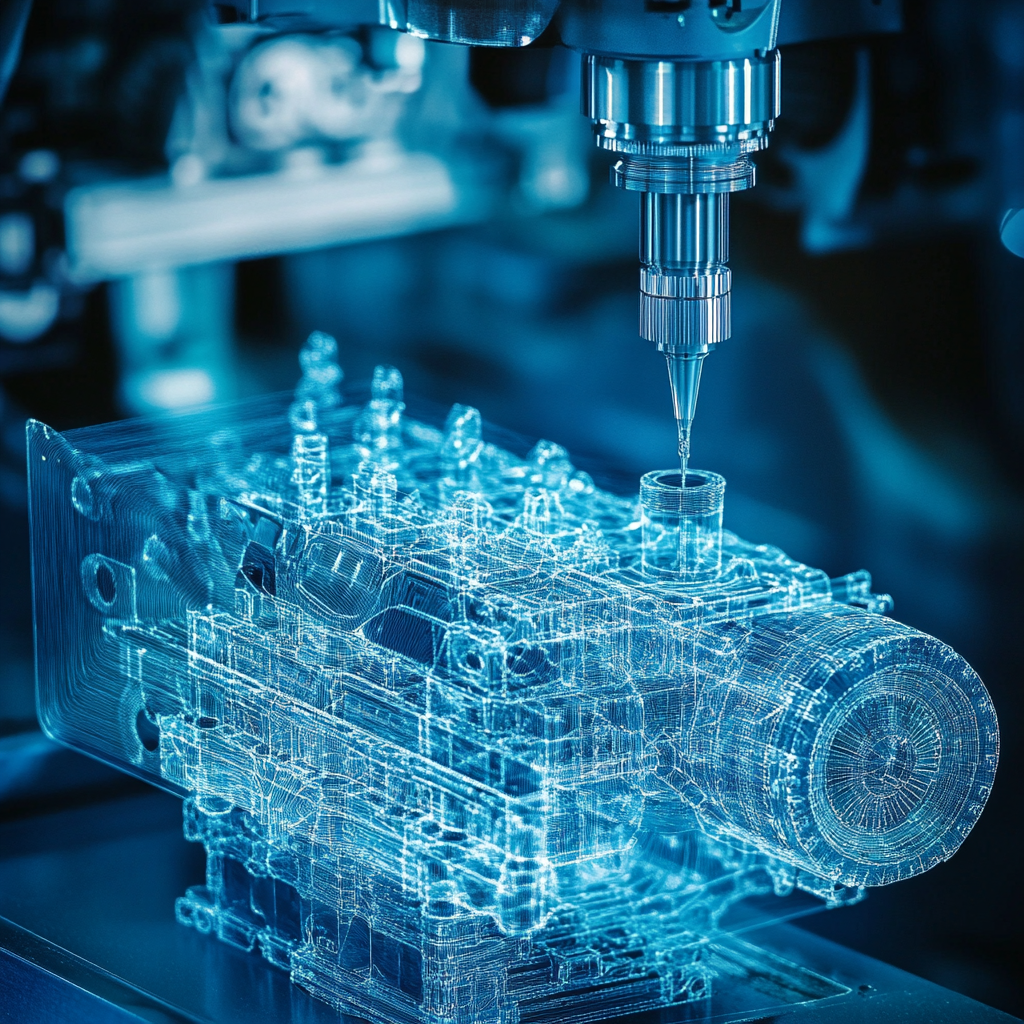
Techniques to Save Money on Manufacturing Your 3D CAD Model
Our team of outsourced CAD experts wants to talk about ways that your engineering team can save money on manufacturing with each 3D CAD model in 2024.
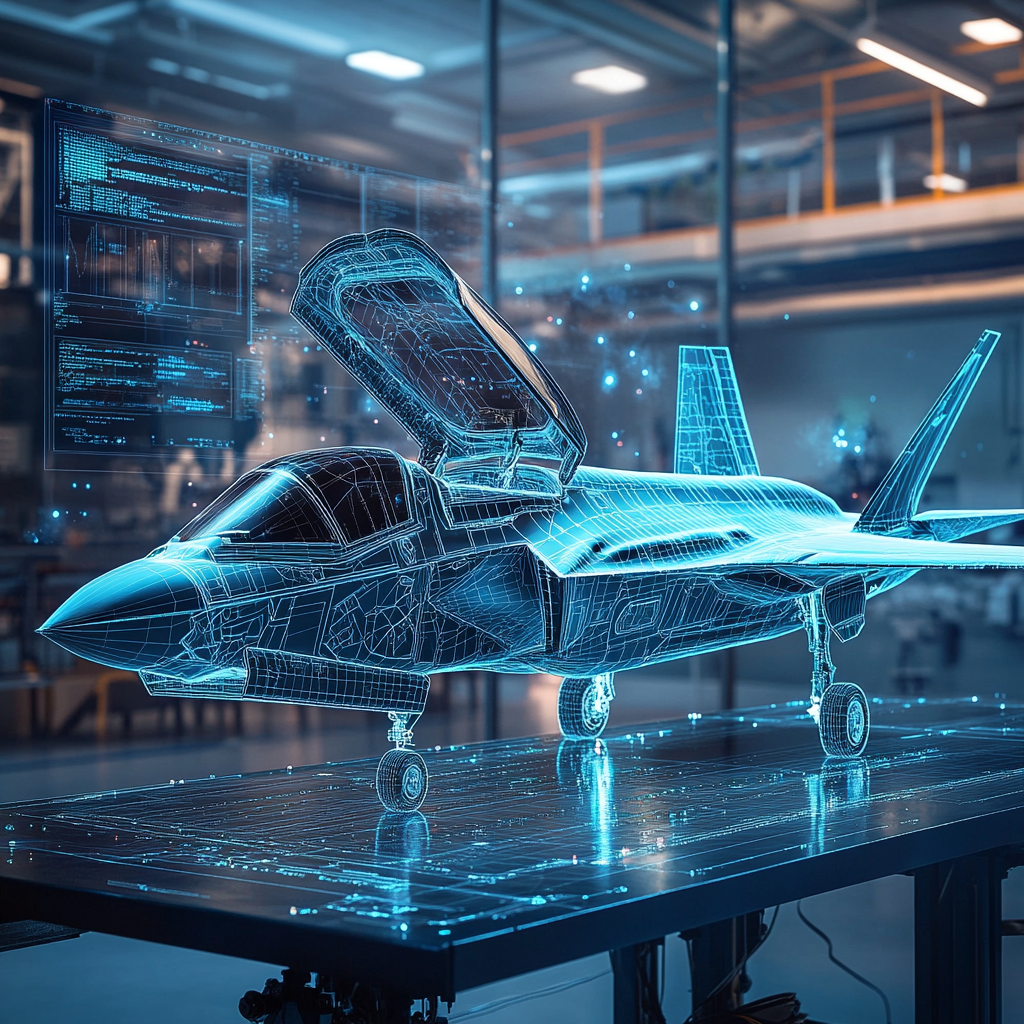
Shortcuts to Save Time on CAD Conversions
a quick tip to save money on each of your CAD conversions