Benefits of Reverse Engineering Tools and Dies
Whether you have one or 100 specialty tools or dies in your shop, you can benefit from reverse engineering. Reverse engineering gives you a lot of freedom and can save you money on your inventory of tools.
This guide will teach you the benefits of reverse engineering tools and dies and we’ll cover how you can quickly and accurately do your reverse engineering.
What Is Reverse Engineering?
Reverse engineering is the process of taking a physical part and creating a 3D model and 2D drawings of it. Typically, reverse engineering is done on parts that don’t have any documentation. This process will create models that you can work from to recreate the part or modify it.
Reverse engineering can either be done by your engineers in-house, or you can bring in an outside expert to handle the work.
As a quick warning: the process is more involved than you might think. It’s not as easy as taking some measurements and making a 3D model. That’s why we always suggest choosing a team like CAD/CAM Services to help with your reverse engineering project.
Why Would You Reverse Engineer Tools and Dies?
The tool and die industry is very nuanced and most parts that you find are highly customized. This is why reverse engineering is extremely valuable in this space — if you have a one-off part in your facility that doesn’t have a model, what are you supposed to do?
Since the part is customized, there’s no brochure that allows you to order a replacement. If you reverse engineer it, you can create your own replacements and even stock up an inventory of spare parts. The reverse engineering process doesn’t care how customized and unique a part is.
Using a 3D Scanner Helps a Lot
There are two common ways to reverse engineer a part. The first way uses a set of calipers and a tape measure. You would fully measure the tool and all of the components. Next, you would take the dimensions to your computer and use your CAD program of choice to model the part. From there, you can create 2D drawings of the model and hope that all of the dimensions are correct.
With this traditional approach, there is a lot of room for error. If you measured incorrectly, made a wrong assumption about the measurement, wrote down or read the numbers wrong, or typed anything incorrectly, the part won’t work. A very simple mistake like this could ruin the part.
This is largely why a lot of companies are using 3D scanners instead. A 3D scanner is like a magic wand that you move around the part and it collects millions of tiny points in space. Instead of magic, it uses a collection of cameras, lasers, sensors, or soundwaves to collect the data.
Those points are then transferred to CAD and processed into a solid part. You’re left with a scaled 3D model of the scanned part on your computer.
3D scanners save a ton of time and remove most of the human error associated with traditional reverse engineering.
The only issue is that 3D scanners are pretty expensive if you want a very accurate one. For that reason, you would likely need to contract this part of the process to a company like CAD/CAM Services. We handle the 3D scanning and model processing to make sure you can reverse engineer your tools and die even quicker.
Benefits of Reverse Engineering Tools and Dies
There are a lot of reasons why people reverse engineer the tools and dies in their facilities. Here are some of the major benefits of doing this.
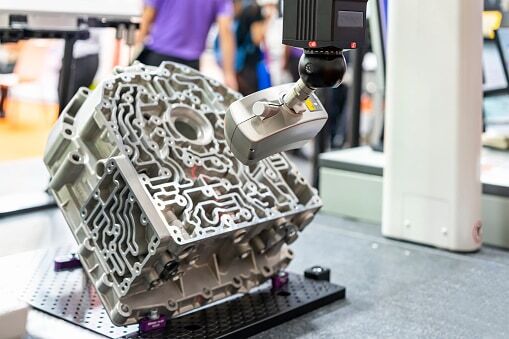
Quickly Make Specialty Tools
Specialty tools and dies are very common. This is when a tool and die manufacturer creates a special, one-off part that is tailored to your specific operation and meets your needs. The only problem with specialty parts is that they can have very long lead times if the shop has to do the design work.
Instead, you could provide a 3D model of the die and speed up the whole process. What might take a shop a few days or weeks to design can be done in your shop within a few hours. This assumes that you’re using 3D scanners and a high-quality CAD outsource team, of course.
Still, this time saving is a huge deal. You don’t even need to be a specialty tool designer to do this process, thanks to reverse engineering.
Save Money on Fabrication
The other huge problem with specialty tool manufacturers is that they’re very expensive. They serve a specific niche, so they can overcharge for their services. Once they make one die for you, they have you locked in and you have to keep ordering through them and overpaying each time.
That is, unless you reverse engineer the tool. Once you have your own 3D model and 2D CAD drawings, you can get a quote from any manufacturer in the area with the right machining capabilities. Since you can shop out the fabrication, you can get a more competitive quote and save money.
In reality, you can save a lot of money by doing this. The savings get even bigger if you have an in-house machine shop that can handle a project like this.
Create an Inventory of Spare Tools
Another benefit of having a 3D model is that you can create as many spare parts as you’d like. If you’re dealing with a high-use die, then it helps to have backups you can leverage. This will greatly minimize your downtime if something happens to your main die. Instead of waiting for a shop to make a new version and send it to you, you can go into your backroom and grab the spare.
As your budget frees up and you learn more about the lifespan of your tools, you might buy even more backups. It never hurts to have an inventory of spare parts that you can rely on.
Redesign a Tool or Die
Do you have a tool or die that you wish was slightly different? Or maybe your flagship product is slightly changing and the new version won’t work on your current die setup. In either case, you can benefit from updating the design of your current tool.
This is where reverse engineering really starts to shine. Since you have an editable 3D model on your computer, you can adjust the tool however you’d like. This could mean adding new interfaces to accommodate your new product, or tweaking the functionality.
You have full access to the design and the freedom to adjust it however you’d like. You can then take your new design and get quotes from a dozen different machine shops before finding the perfect partner.
The bottom line is that reverse engineering your tool or die gives you a lot of freedom and untethers you from the original tool manufacturer.
Conclusion
As you just learned, reverse engineering a tool or die can save you a lot of time and money in the future. If you need help with 3D scanning or designing, feel free to reach out to our team at CAD/CAM Services. We are a full-service CAD design team that can handle your reverse engineering project. Get a free quote today.
Recent Posts
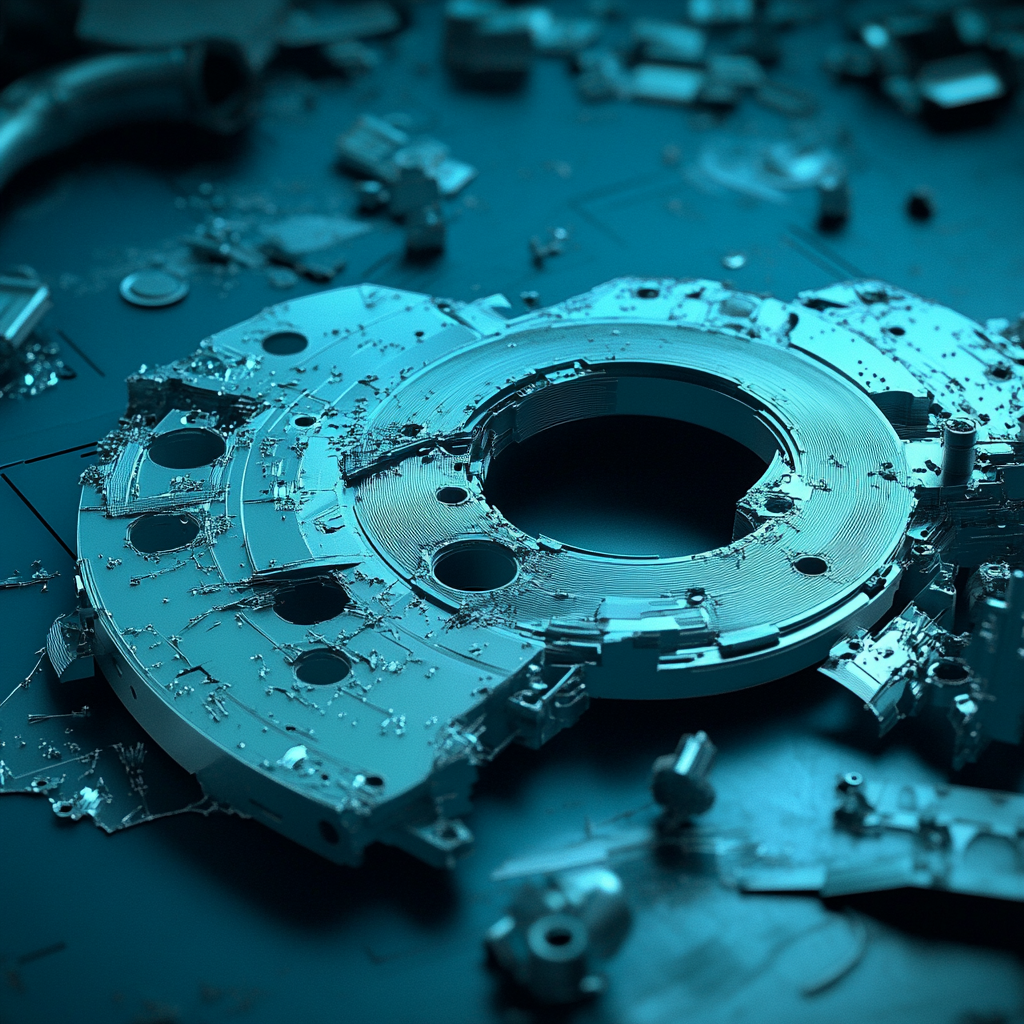
5 Common CAD Mistakes and How to Avoid Them
We came up with 5 common issues that we see, and our expert advice when it comes to avoiding these issues.
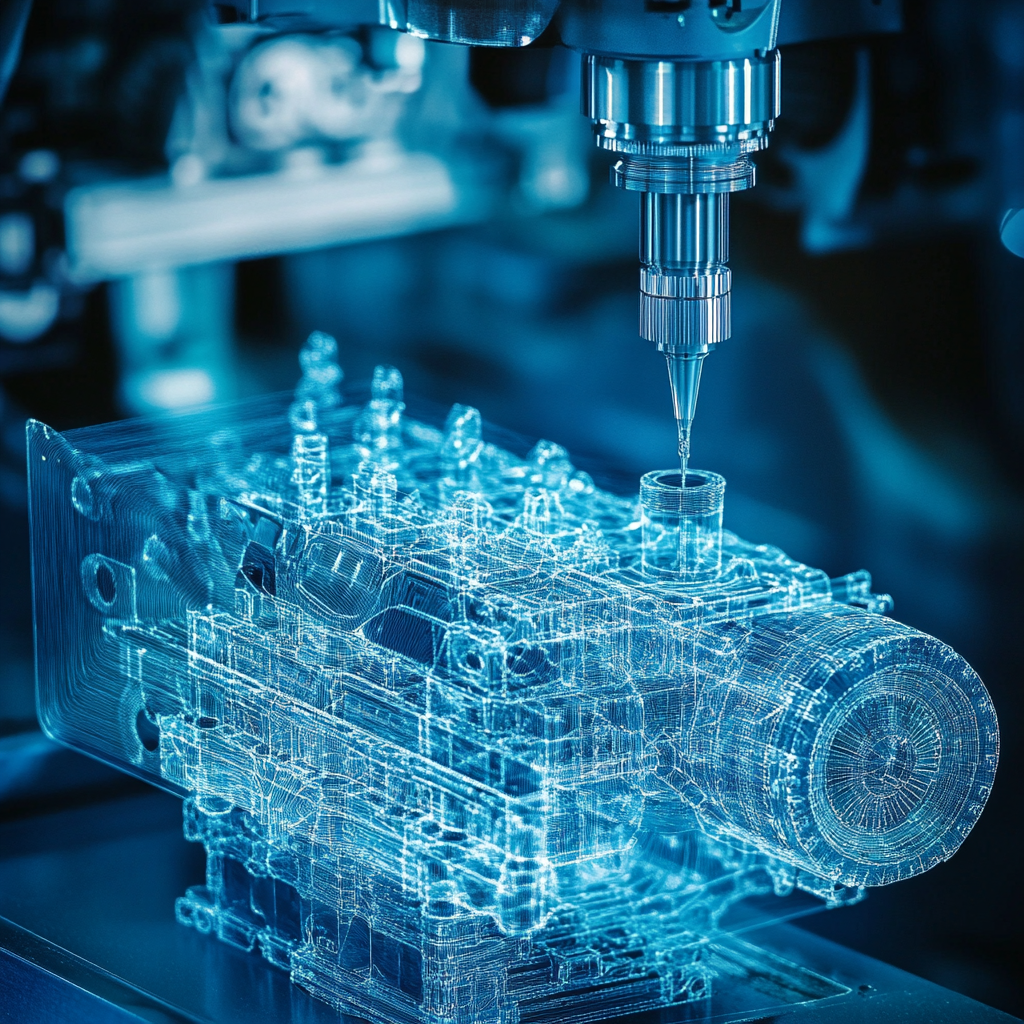
Techniques to Save Money on Manufacturing Your 3D CAD Model
Our team of outsourced CAD experts wants to talk about ways that your engineering team can save money on manufacturing with each 3D CAD model in 2024.
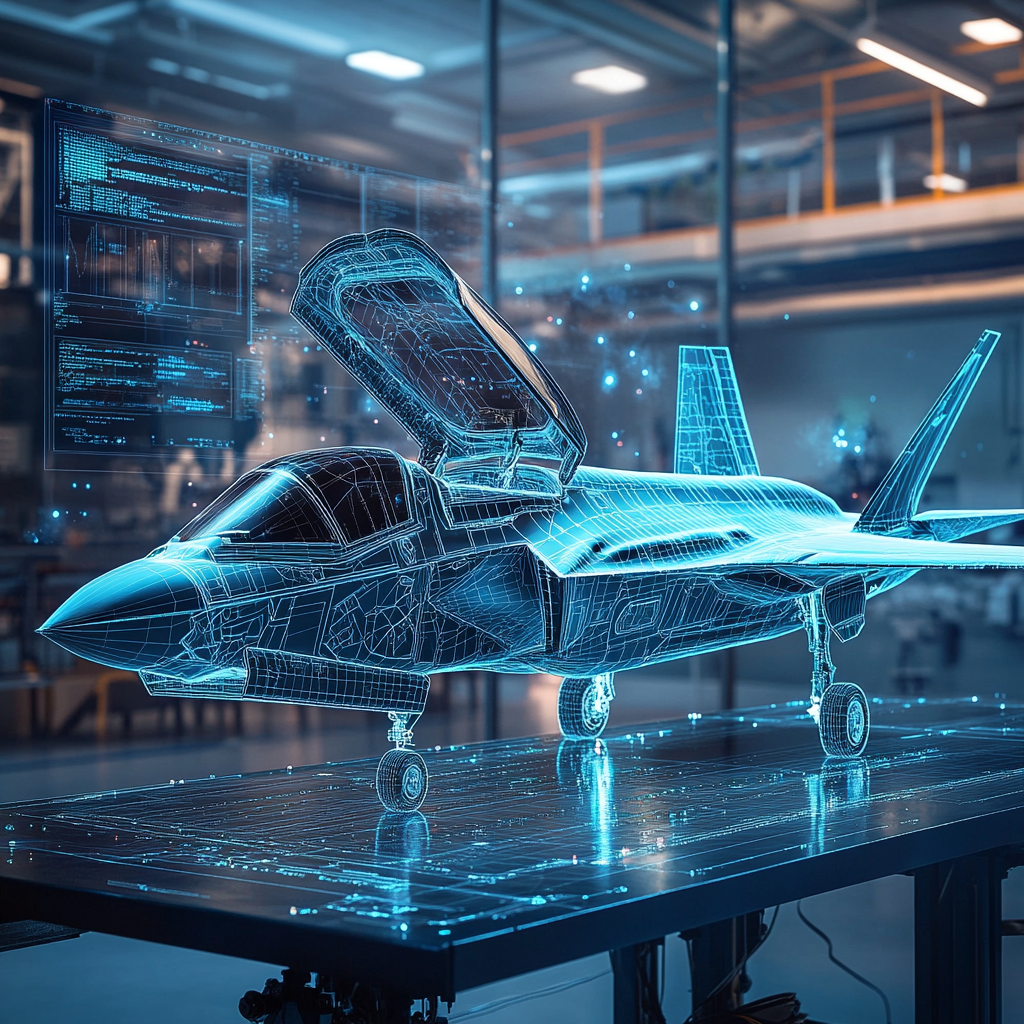
Shortcuts to Save Time on CAD Conversions
a quick tip to save money on each of your CAD conversions