Why Digital Twins Are Revolutionizing Product Design and Development
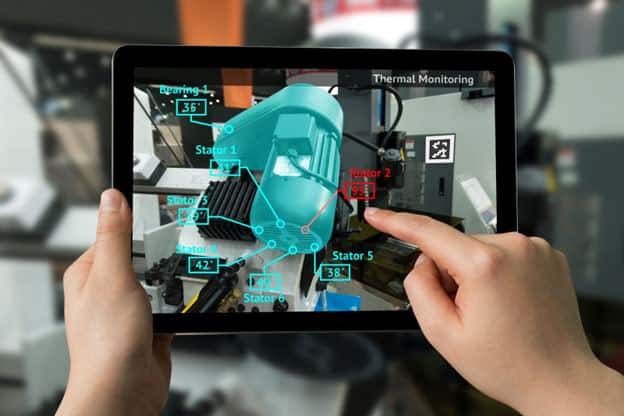
The idea of a digital twin is a relatively new one. Since 3D CAD became popular, companies are realizing that they can optimize and streamline their product design and development efforts. How is that possible?
In this guide, we’ll explain how and why digital twins are revolutionizing product design and development. We’ll include real-world examples and show you how you can benefit from a digital twin.
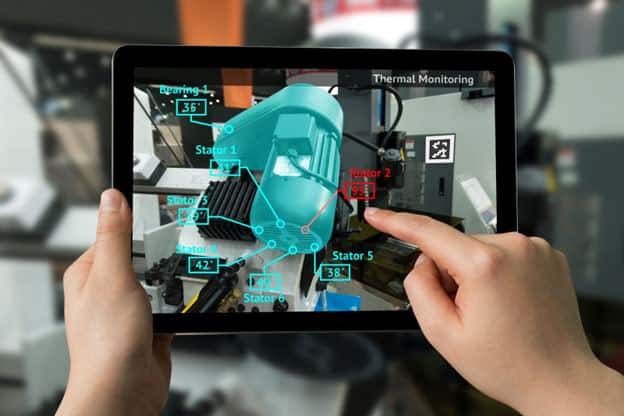
What Is a Digital Twin?
A digital twin is a digital version of a physical object. The object could be a part, process, operation, or whole manufacturing facility. In most cases, the digital twin is made in a 3D CAD program and the physical part is measured or scanned in real life.
If you take a bracket, measure it, and draw it on Siemens NX, you just made a digital twin. The same is true if you 3D scan your entire production warehouse and push the model to CAD.
When to Use a Digital Twin
There are a number of reasons why you might use a digital twin. People will digitize their current operation if they’re looking for performance bottlenecks or they want to update their process.
You might make a digital twin of a machine if you’re looking to retrofit a piece — by making the twin first, you can look at clearances and fitment before making the part.
Here are two real-world examples that we’ve encountered in the past:
One customer wanted a digital twin of their plastics processing plant. They had one line that was making a flagship product and they wanted to add a second line in the same warehouse.
Our digital twin included the warehouse itself, storage area, machinery, structural steel, walking platforms, and all of the equipment used in their current operation.The digital twin included everything.
Every part was drawn or scanned into 3D CAD, and everything was to scale on the screen. This allowed us to move their machines around on the screen without needing to physically move the machines.
Another customer we had owned a recycling plant and they wanted to upgrade one of their bottle grinders (those big machines with rotating teeth that eat whatever bottle you throw in, turning it into chips of plastic or glass).
They wanted to add a larger chute and the grinder supplier wouldn’t help them. We modeled their machine and added larger interfacing brackets which allowed them to modify the chute.
In this case, the digital twin was the machine: all of its bracketry and every part of the assembly. We used this twin to figure out how to change the chute and enhance their operation.
In either of these examples, you’re seeing what a digital twin does and how it works. Now, let’s look more broadly at how this idea can help with your design and development of parts.
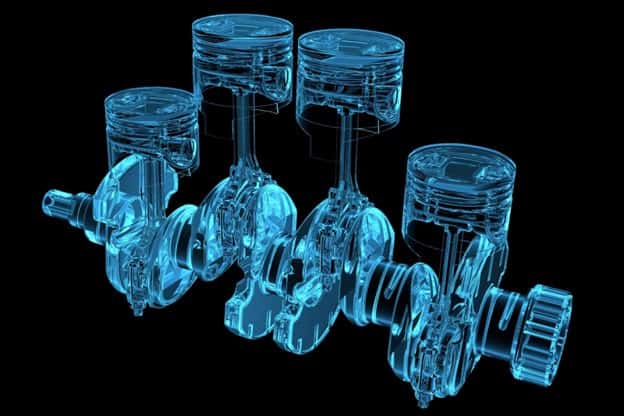
How Digital Twins Help with Design and Development
There are a lot of ways that digital twins can help your business. We can provide specific feedback through a phone call or email, but we’ll keep things more general in this section. Here are four ways digital twins help with design and development.
Faster Development
As much as we love the “guess and check” technique, it typically doesn’t work in engineering when it comes to development. Whether it’s a product that needs to fit into your operation, a changing layout on the floor, or an upgrade of an existing machine — you’ll develop everything much faster if you have a full digital twin.
With a 3D model, you can perform quick tweaks on your machine, move it around, and re-orient the machine without needing to leave your computer. There are plenty of times when it helps to see things on the screen so you can realize potential issues.
You might think that adding a handle to your new container will help move it around. However, the digital twin could show that the handle interferes with nearby tables.
You can spot this in five minutes on the screen, but you wouldn’t notice until it was too late without a digital twin.
Optimize the Design
It’s so much easier to optimize a design when you do it on a digital twin. Let’s say you want to design a custom glovebox. This will be put in your chemical processing plant. Operators will use this glovebox to safely open and interact with dangerous chemicals.
There are a few design features that you might be able to do without a digital twin: where the glove access goes, how the legs are configured, and some general structural decisions.
But, how do you know that your chemical containers will fit perfectly into the glovebox? Are you positive that you’ll have the right access within the box so an operator can interact with the chemicals? Where will the fume hood take the toxic gas?
All of these questions can be answered immediately with a digital twin. You can insert 3D models of the chemical containers, nearby exhaust system, and even add a 3D model of the operator using the glovebox.
Your design can be optimized, and you’ll have more confidence. You might find that the fume hood should be designed in a different way to miss overhead restrictions in the facility — something that you might not notice without a digital twin.
Better-Prepare for Gate Meetings
As an engineer, you probably have to go through a series of alignment and Gate meetings before you can start making your new product. These meetings can get tough, but digital twins can actually help you through them.
Stakeholders will undoubtedly have questions about sizing, fitment, material choices, weight, and so on. Most of these questions can be addressed with digital twins.
The digital twin can include material properties which give you an accurate mass and center of gravity. You’ll also have 3D renderings that you can show during the meetings.
This allows you to point to features, explain your product, show the fitment, give a reference for sizing, and justify the need for it.
With a digital twin, you can put your proposed part directly in the warehouse and show stakeholders exactly what you’re talking about.
Easier Product Manufacturing
Having a machine shop fabricate or 3D-print your part is exponentially easier when you have a digital twin. You can quickly cut 2D drawings out of the model and send them to shops. With 3D printing, you would send the digital twin to a printer, and they’d get to work.
Since everything is drawn in a 1-to-1 scale on a digital twin, it’s ready for manufacturing. Providing the 3D model to a machine shop can avoid phone calls and headaches during the fab process.
Conclusion
Digital twins are currently the best practice for most product design and development projects. You can save time, optimize your design, make things easier for the manufacturer, and streamline review meetings.
To start with your digital twin today, reach out to our team at CAD/CAM Services. We are a full-scale drafting team that can create digital twins of your products for your upcoming projects.
Recent Posts
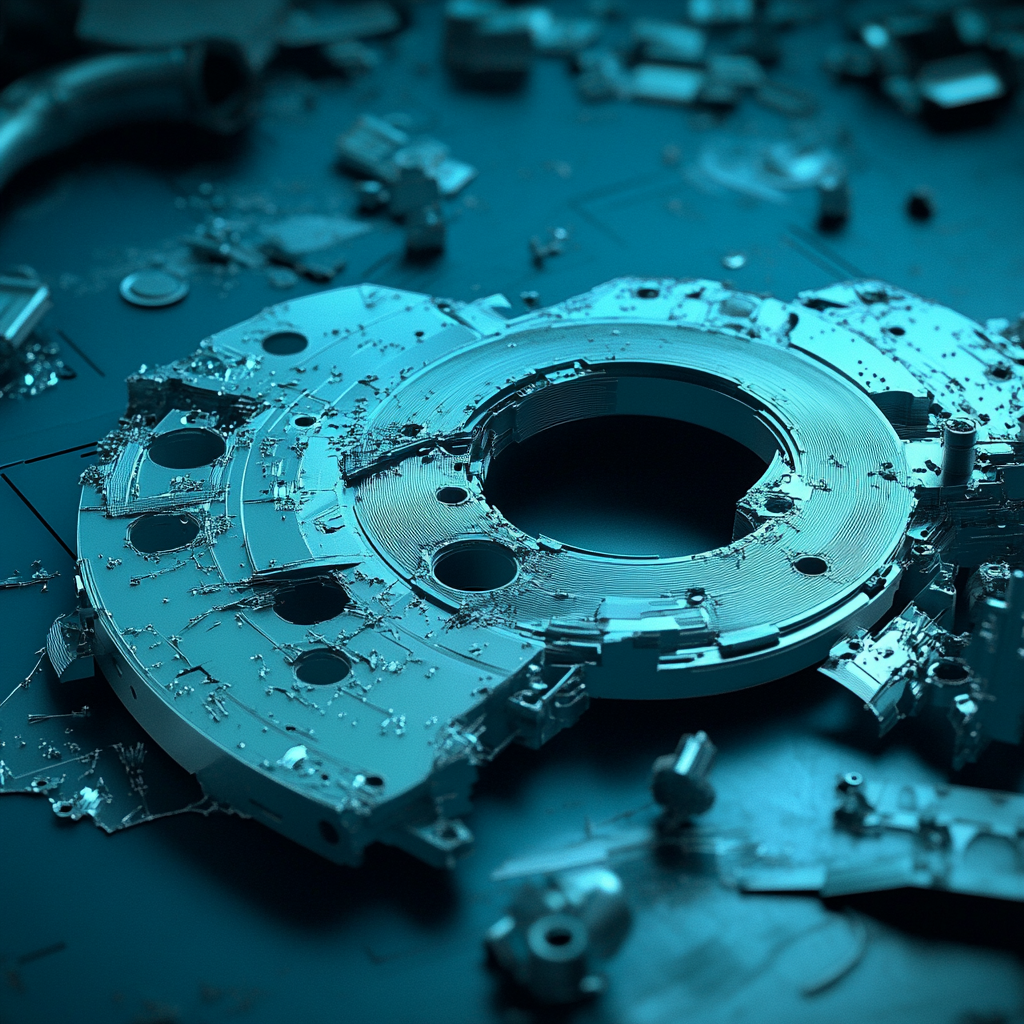
5 Common CAD Mistakes and How to Avoid Them
We came up with 5 common issues that we see, and our expert advice when it comes to avoiding these issues.
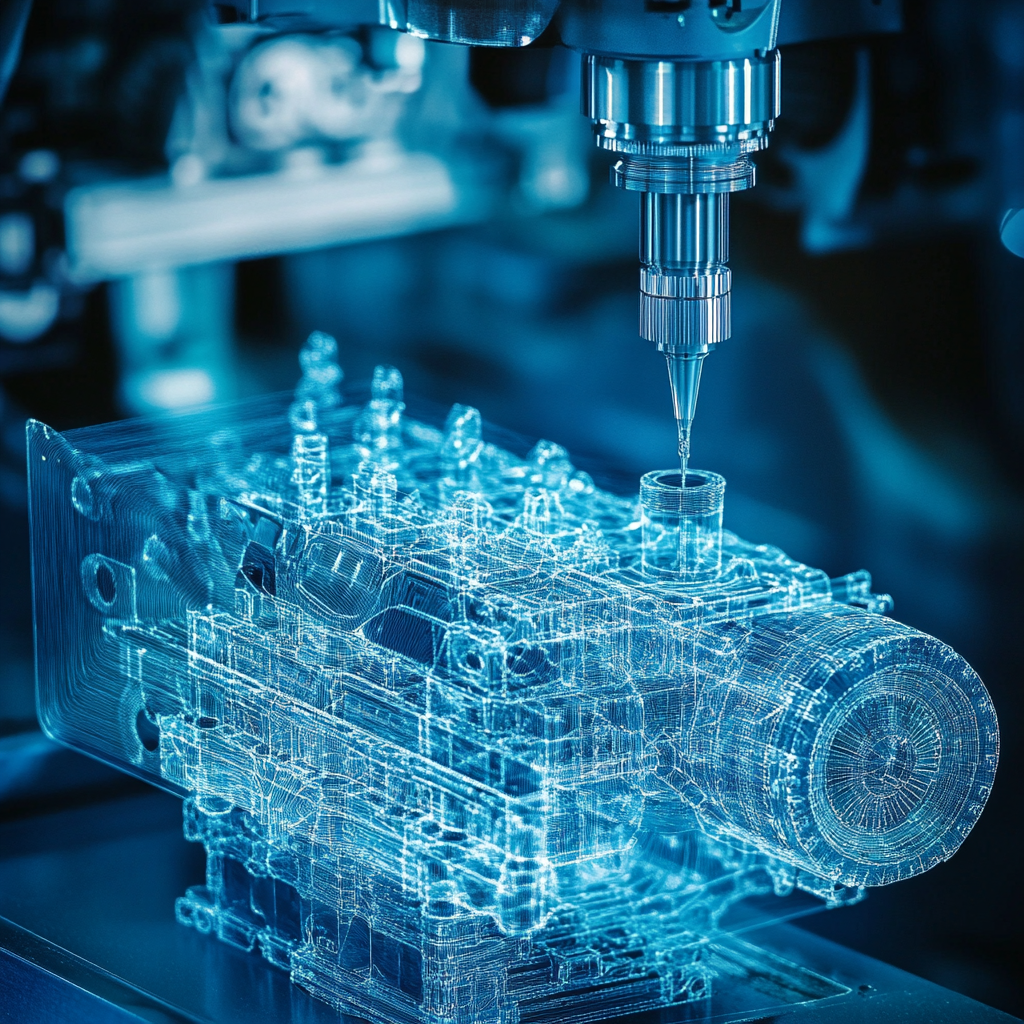
Techniques to Save Money on Manufacturing Your 3D CAD Model
Our team of outsourced CAD experts wants to talk about ways that your engineering team can save money on manufacturing with each 3D CAD model in 2024.
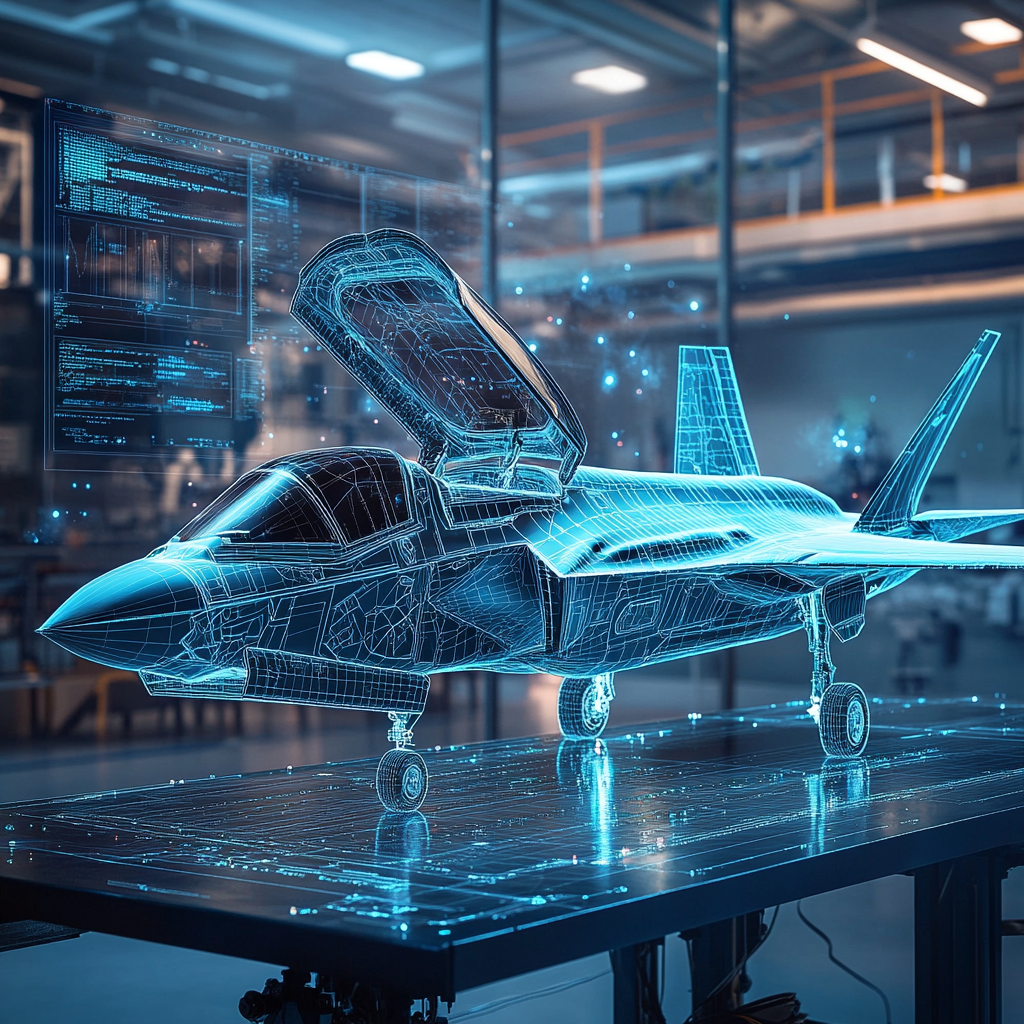
Shortcuts to Save Time on CAD Conversions
a quick tip to save money on each of your CAD conversions