Case Studies
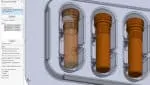
Our client
A producer of various medical appliances and accessories.
Task
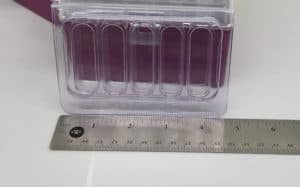
The client called us to improve the existing design of the tube holder. They had one in their possession already. We had to deliver modified 3D CAD models. Normally reverse engineering is a process that starts with 3D scanning in order to recreate the initial 3D design before applying any modifications.
This time everything was different and by different, we mean cost-effective. In order to save the client’s time and money, we decided to skip the 3D scanning part as well as working with point clouds.
Solution
Fortunately, the tube holders are rather common consumer products, so it is easy to imagine one without any special preparation. So we decided to solve this problem using a remote reverse engineering. Our client provided us with the tube holder photo, tube dimensions, and the required number of tubes for each of the tube holder models.
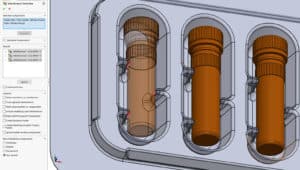
The example holder was designed to contain 5 tubes. We had to create 3D models of tube holders for 7 and 12 tubes.
This kind of typical task is best solved with SolidWorks 3D CAD software. During the design process, we created the 3D model of a tube. After that, we performed a series of interference detections with SolidWorks standard interference detection tool in order to see if the tubes will sit tight in their positions. We also tested the lid in a closed position.
These steps allowed us to instantly provide our client with a suitable model without the need for any revisions.
Results:
Good design is CAD Perfect™ design, so our model was good to go.
Our customer was completely satisfied with the very first set of models we provided.