BIM Conversion – Steps for Turning 2D Drawings into 3D Models
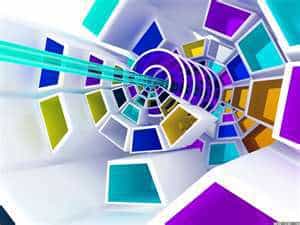
BIM conversion can be a huge undertaking for any organization that has large numbers of drawings. Yet, more and more, 3D is the way to go, so manufacturers, architects, and others are looking at ways to convert their legacy paper drawings or CAD drawings into 3D BIM Models.
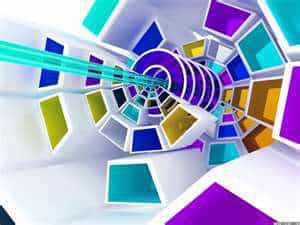
This 3D future is clear, but getting it is not always easy. If you recall the transition from hand-drawn plans to CAD engineered drawings, you will remember the pain of moving from one era to another. While CAD was not nearly as significant a change as BIM is proving to be, CAD changed how we designed, changed our processes, and changed the economics of design firms. Multiply this by many times and add in manufacturers, contractors, owners, and operators as integral parts of BIM you will begin to understand the true impact of BIM.
Yet, it’s true that even the longest journey begins with a single step…or, in this case, four steps that we’ve identified as “must do” when converting 2D drawings to 3D BIM models.
- Filter Data – Design data that were created in a 2D CAD program can usually be converted into a 3D CAD data. Generally, data such as dimensions, line type parameters and layers are filtered before being imported into a 3D BIM system. The filtering process usually results in accurate conversion from 2D to 3D.
- Identify Projected Geometry – For seamless data transition from a 2D CAD package to a 3D parametric CAD tool, it is essential to enable quick and accurate orientation of data from various views. (A 3D model can be viewed from six different orientations.) This process is established by orienting various views into a box, which provides all three planes — XY, YZ, ZX.
- Align Various Geometric Views – The basic views necessary for the creation of a 3D Model should be identified first since orientation and alignment are important for extruding the 3D model. These alignments can be carried out using a basic translation technique which usually includes only a command to move to the appropriate plane. This is the best way to ensure an accurate 3D model.
- Extrude (Boolean operation) — This process guards the final 3D Part model against errors and makes it ready for use. The person doing the converting must use the sketch properly, since, once used for extrusion, the sketch cannot be used again. Cutting and intersecting is generally used for arriving at the final model
Because of the precise nature of the steps required to convert the 2D drawings to 3D BIM models, it is recommended that a professional outsourcing firm, familiar with the intricacies of the process be used. This is generally more cost-effective and more efficient than using internal CAD operators, whose time is better spent on new designs rather than legacy conversions.
Recent Posts
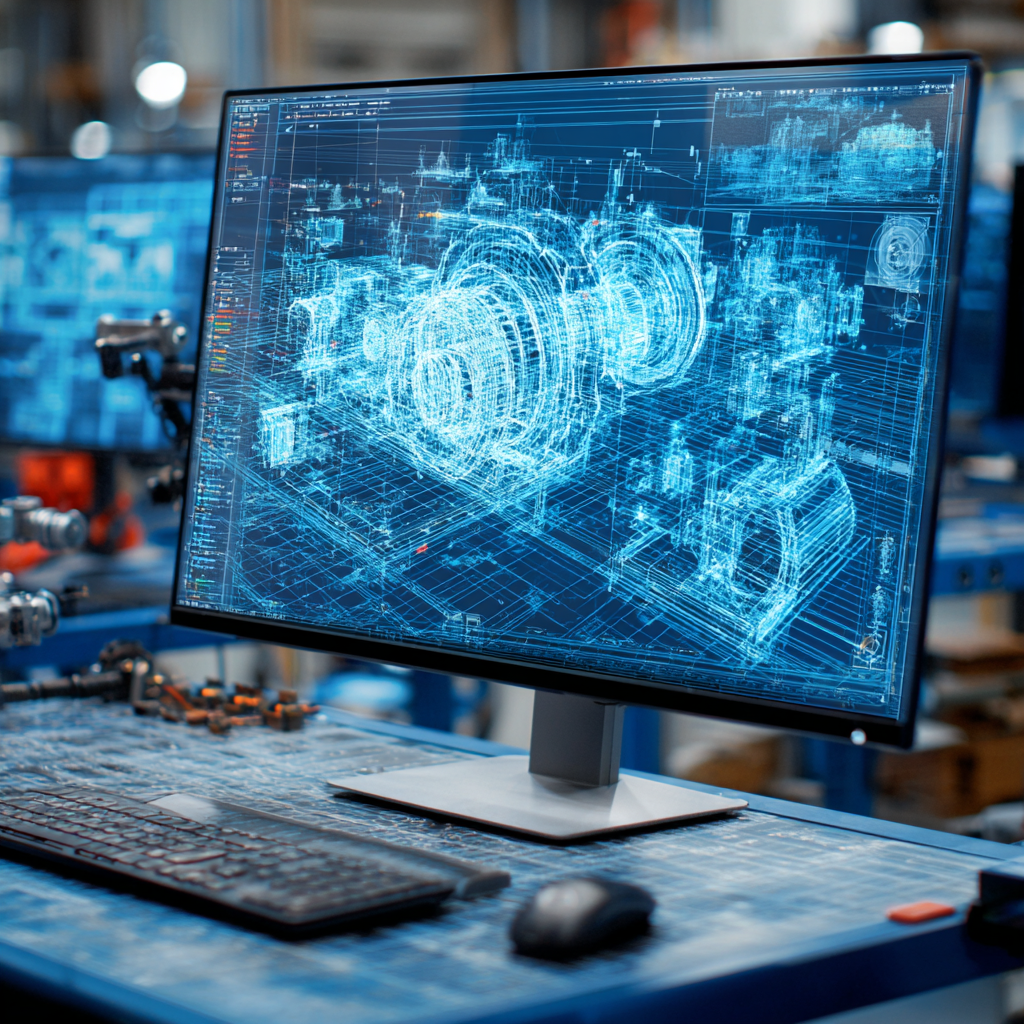
Tips for Picking the Perfect 3D CAD Viewer for Your Needs
This guide will teach you about 3D CAD viewers and outline considerations to make before picking the right one. We review 5 options and pick a clear winner.
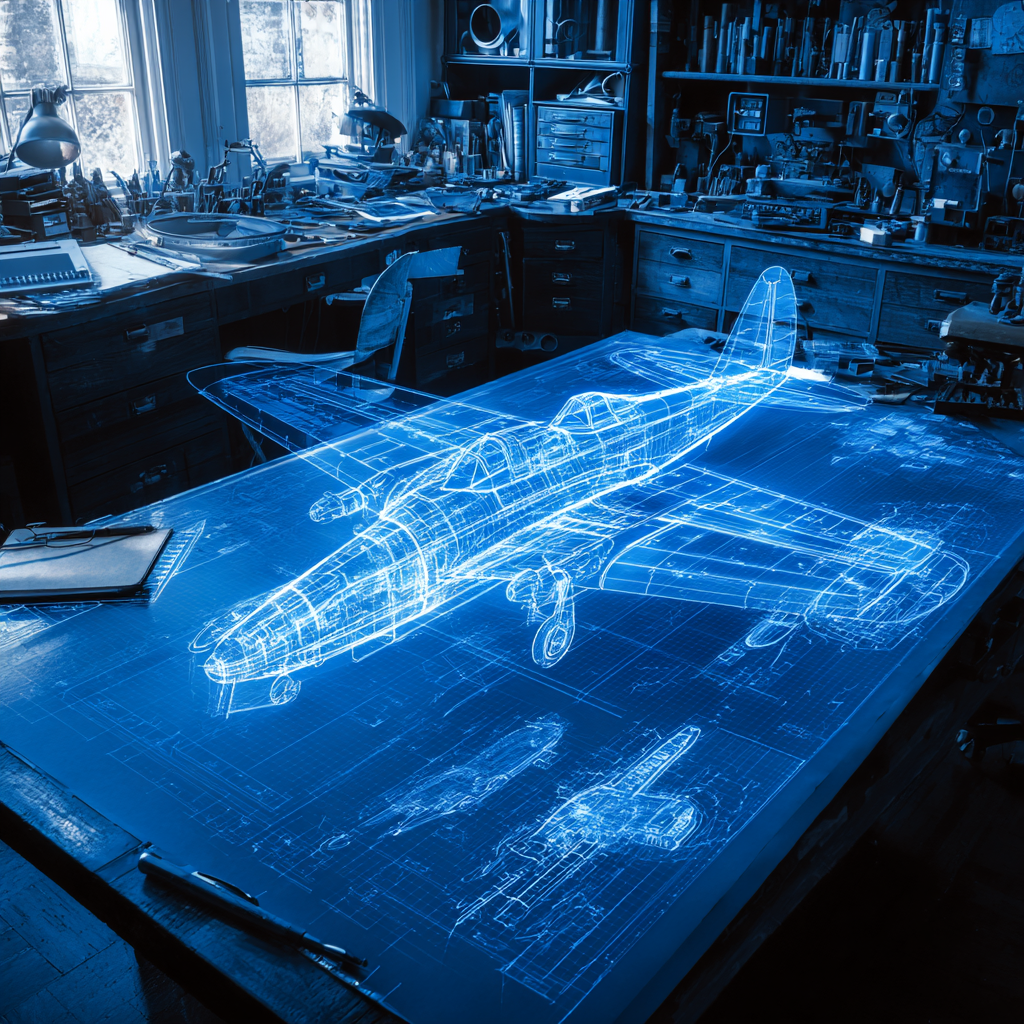
In this guide, you’ll learn how CAD/CAM Services can save you time and money during each digitization project. Digitization can make manufacturing faster than ever before.
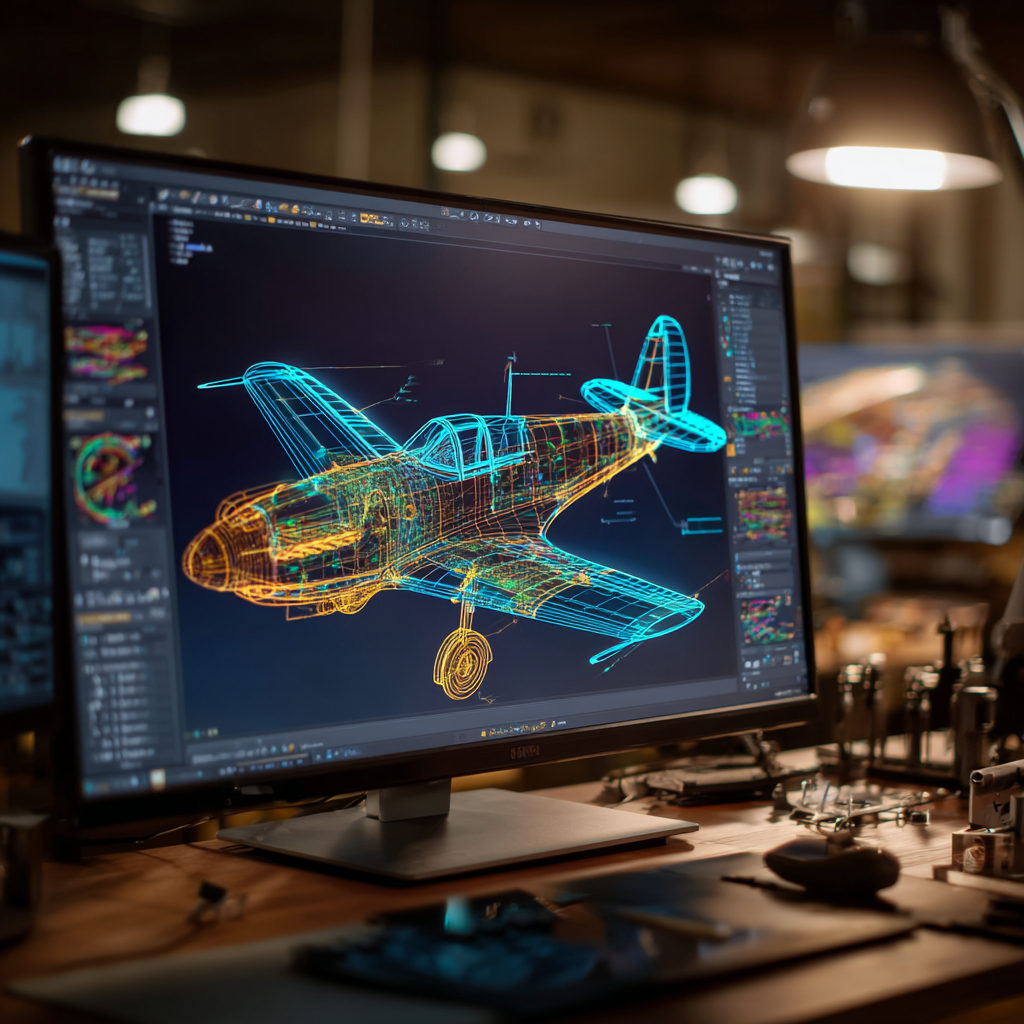
How to Build an Aircraft Model by Converting 3D-Scanned STL Files into Functional 3D STEP Files
This in-depth guide will teach engineers how to use 3D-scanned aircraft files and transform them into manufacturable 3D STEP files with fewer mistakes.