CATIA Draft Analysis: A Beginner’s Guide
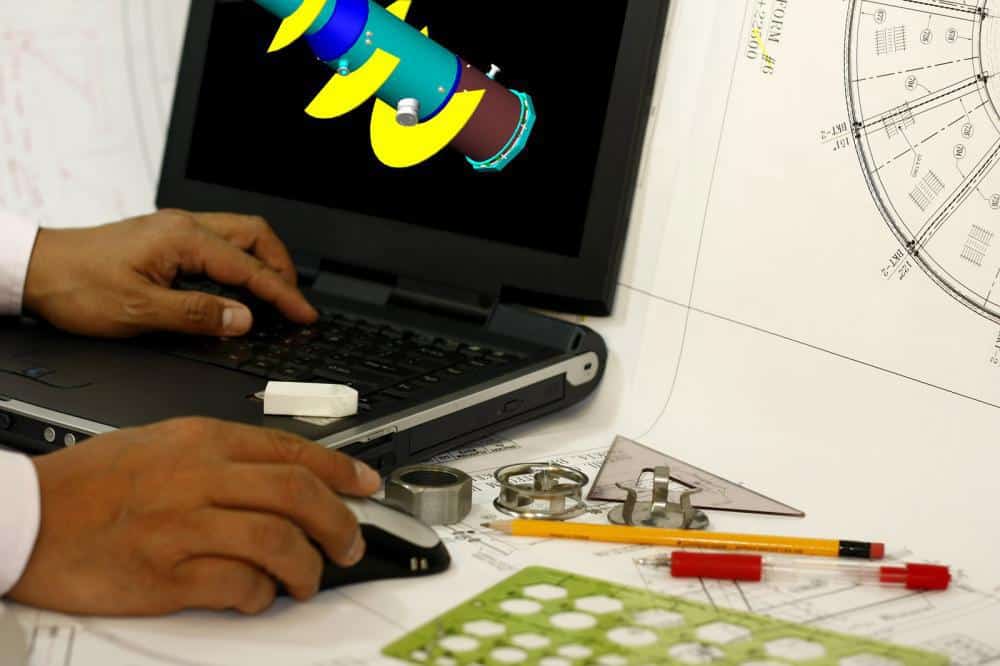
CATIA’s innovative CAD software allows users to create a wide range of precision parts quickly and effectively. But while CATIA’s modeling tools may allow you to check the functionality of your finished components, you must also ensure that your parts can be successfully removed from their molds. With CATIA Draft Analysis, draft angles can be evaluated and optimized for your design for easy ejection. Here is a brief guide on how to make use of this intuitive feature.
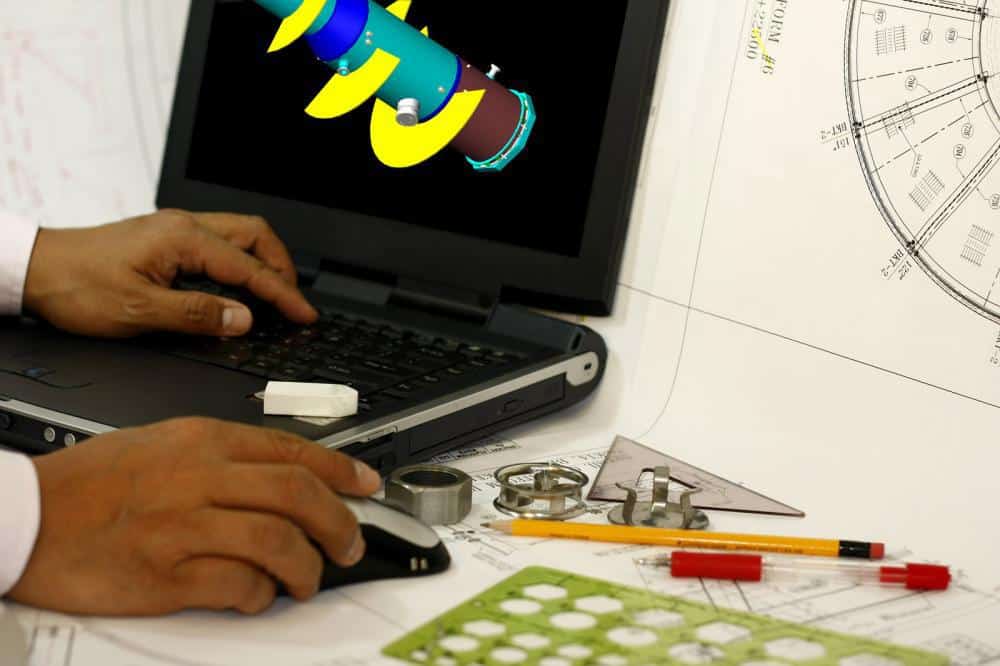
The Keys to CATIA Draft Analysis
To begin, you need to have a finished 3D model in CATIA’s Workbench. From here, you enter “Material Mode” and access the CATIA Draft Analysis box. Amongst other details, the box will show the color scale and the upper and lower limit values for draft analysis. With this tool, you can determine whether your draft angle is positive or negative and thus where the parting line and/or shutoff for the part should be. We use these insights to specify surfaces, pull direction, and the draft angle required during the physical prototyping stage.
The analysis tool works by assigning different color ranges to the 3D model. By following these signals you can confirm that draft directions at each point fall within the specified parameters for your part. These parameters can always be adjusted through the unit settings. It is important to note that color accuracy can vary according to the video card used, so if you’re seeing a color representation that doesn’t match up to the stated values then this may just be a display error.
You can perform a draft analysis on any surface of your model. In order to select a surface, check the “On the Fly” box and hover over the intended surface. Once you have highlighted a surface, corresponding details will show up in the draft analysis box. The parameters option should show the direction in which the component will be ejected from its tool. The pull will always be perpendicular to the plane of your surface. You can click the Inverse button to reverse the draft direction.
Once the direction has been set you can set minimum limit against which the draft angle will be measured on various surfaces. For example, if you set this parameter to 3 degrees then all surfaces with an angle of 3 degrees or higher in the direction of the pull will show up as positive, while all surfaces with an angle of 3 degrees or higher away from the pull will show up as negative. You can see the colors that correspond to each value in the quick mode option box.
Remember, there will always be a negative and positive face to your part, your sole purpose here is to identify any surfaces that require further adjustment to fall in line with their corresponding plane.
As you can see, there’s a lot to unpack when it comes to CATIA Draft Analysis. For more information on how we provide outsourced CATIA design services or an estimate on our CAD services feel free to contact us. We’re always ready to help.
Recent Posts
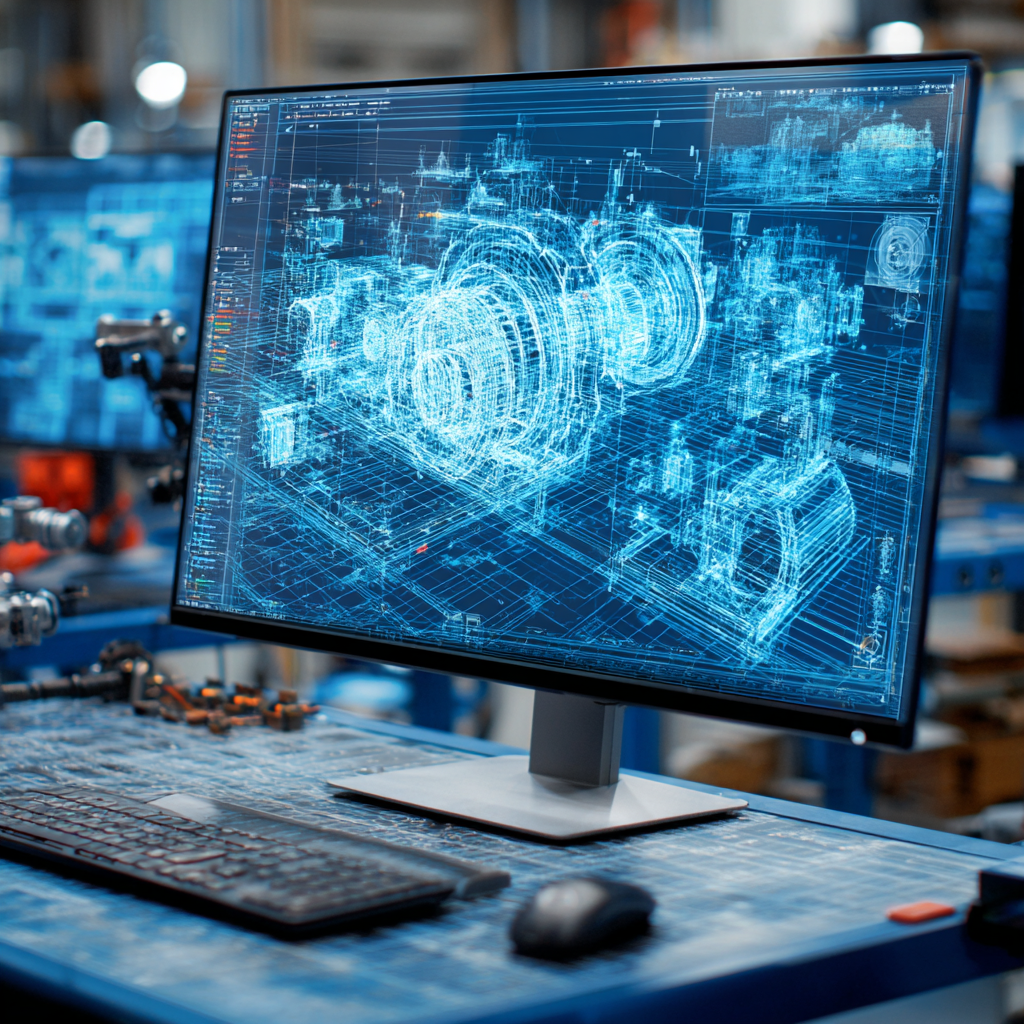
Tips for Picking the Perfect 3D CAD Viewer for Your Needs
This guide will teach you about 3D CAD viewers and outline considerations to make before picking the right one. We review 5 options and pick a clear winner.
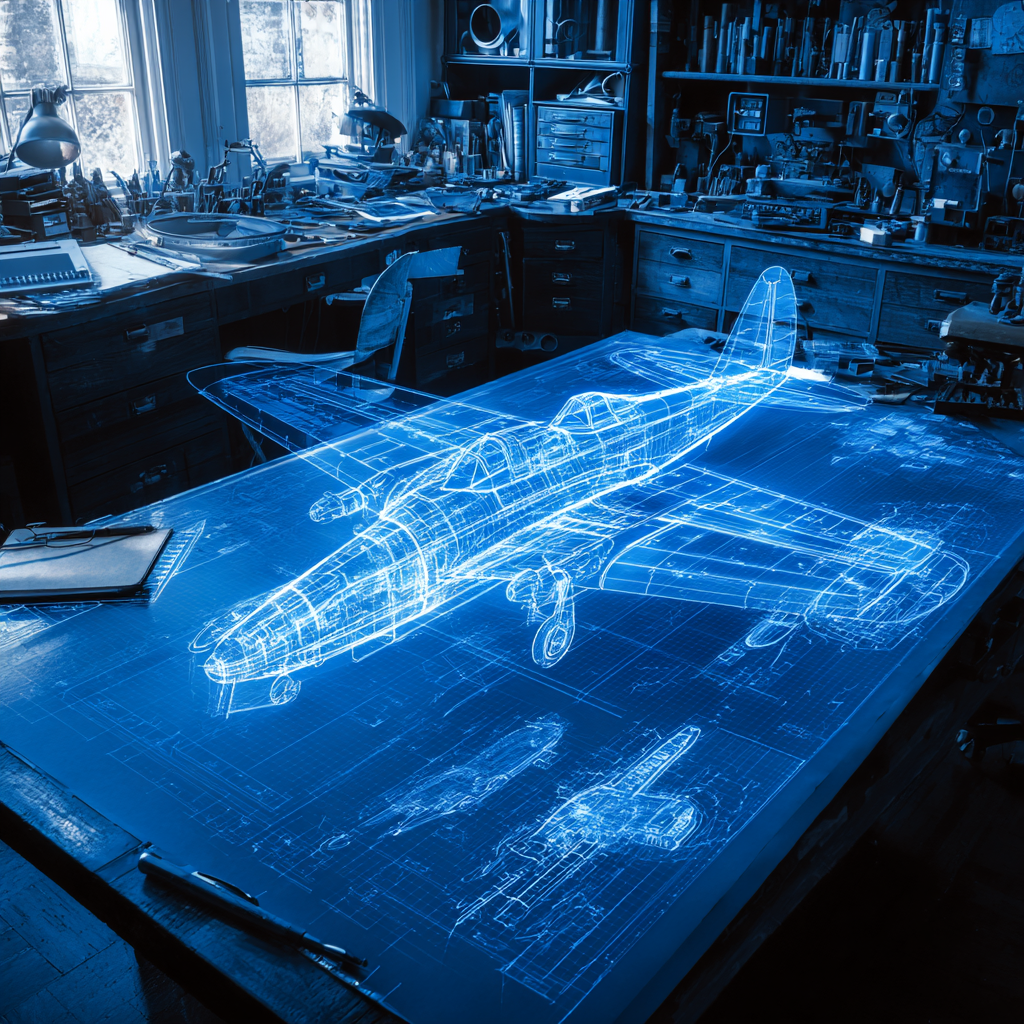
In this guide, you’ll learn how CAD/CAM Services can save you time and money during each digitization project. Digitization can make manufacturing faster than ever before.
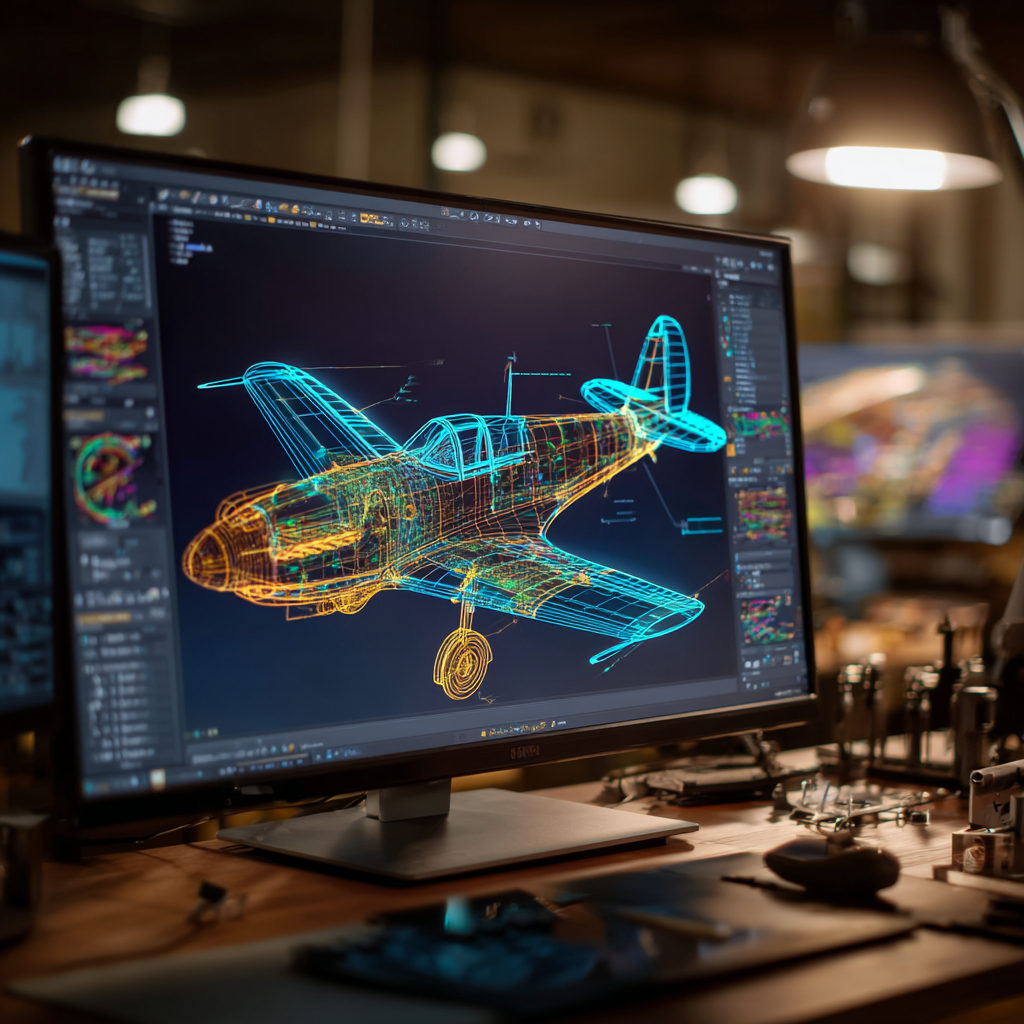
How to Build an Aircraft Model by Converting 3D-Scanned STL Files into Functional 3D STEP Files
This in-depth guide will teach engineers how to use 3D-scanned aircraft files and transform them into manufacturable 3D STEP files with fewer mistakes.