How 3D Printing Can Increase Efficiency for Injection Molders
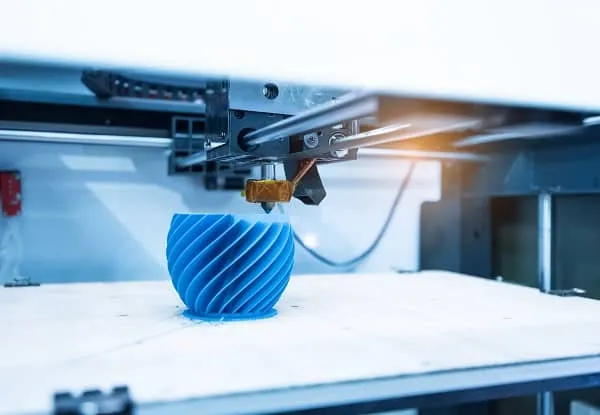
3D printing is great for quick and affordable prototyping, but it’s a poor choice for full-scale production — people use injection molders for that. Even though 3D printers and injection molders cover both ends of the spectrum, there can be some overlap between them.
In this quick guide, we’ll explain how 3D printing can increase efficiency for injection molders. We’ll specifically look at some ways you can save time and money during the process.
A Quick Overview of 3D Printing and Injection Molding
You might already know this, but 3D-printed parts are typically the best option during the prototyping phase. Anytime you’re bringing a new part to market, improving on a design, or adding a part to your operation, there’s some level of prototyping required.
People will usually start with 3D-printed parts so they can quickly make metal or plastic parts at affordable prices. You can go through an iterative design phase without blowing your budget or adding months to your lead time.
Once the design is perfected, then you’re ready for injection molding. Injection molders require molds to be machined. These molds and inserts regularly cost hundreds of thousands of dollars, and take months to fabricate. Once they’re made, they’re basically final.
Making major changes would involve spending the same amount of money and waiting again. Before making the mold, you need to validate and freeze your design.
Once the design is finalized and matured, injection molding is likely your best choice for high volume production. You can make parts for pennies, and a machine can create a production-quality part within a few minutes. These machines can run all day with very little supervision.
In very large quantities, injection molding machines outperform other manufacturing processes. 3D printers can’t run fast enough to keep up with the demand, and their per-unit price never goes down to the level of injection molders.
Whenever a company needs to deliver millions of units a year, they choose injection molding. Now, how can 3D printing and injection molding be used together?
A Quick Fitment Check
Let’s say you’re making a new phone case and you want to check the fitment on your phone before ordering and paying for 10,000 cases. You can certainly use 3D CAD to check out the interference and fit of your part, but tolerances and external factors might not be accounted for.
We’ve seen it too often: a 3D model looks perfect on the screen, but it doesn’t work in real life. There could be measurement issues, drafting mistakes, or tolerances that you couldn’t predict.
Simply put, it’s always best to check fitment with a physical part. Before paying your injection molding company, you should 3D-print a version of your part and check its fit in the actual part, operation, or assembly.
It’d be best to use additive manufacturing to make five units or so. Test them out and see how they fit. This will give you a better understanding of how tolerancing can affect the results. Once everything looks good, then you can order the mold.
3D printing allows you to quickly make physical parts that can be used for fitment checks.
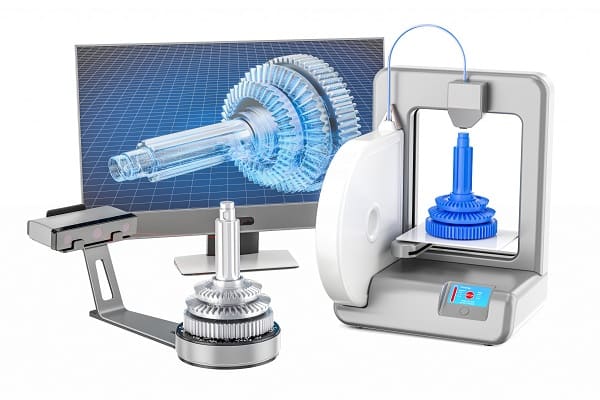
Perform Destructive Tests on Prototypes
Another huge part of the prototyping phase is all the tests you need to do. If you need to do pre-production screening and documentation, then you’ll probably need to run tests. How do you know that the final part will stand up to forces and only fail at a certain load? An FEA is a good place to start, but that’s another example of a theoretical result that doesn’t factor in real-world parameters.
Instead, use a 3D-printed part.
With a box of 3D-printed parts, you can go through a series of destructive tests. By finding out when the part fails, you’ll know how much force can be safely loaded, and what your factor of safety will be.
Since each part costs a few dollars and can be made in hours, it’s not a big loss. You can also go through elongation, thermal, and cyclic tests. By doing these tests ahead of ordering a batch of injection-molded units, you can boost your confidence. You’ll know for a fact that the parts will work perfectly.
If you skip the testing process and don’t 3D print anything, then you’ll still learn that the part is under-designed. The problem? It will be too late. At that point, you already paid your injection molder $100,000 or more that can’t be refunded.
3D Print the Mold Inserts
Some people choose to 3D print the actual mold or insert used in the injection molding operation. You’ll have to chat with your injection molding vendor first to make sure they accept and can use third-party molds in their machines.
If they do accept this, then you can save a ton of money. DMLS printers are metal 3D printers. You load a 3D CAD model right into the machine, and it creates a titanium, aluminum, or stainless steel version of your part.
In this case, you’ll be metal 3D printing the mold that gets put into the injection molding machine. The part you print will have a negative cavity of the final part (make sure you design it using the best practices for cavity and mold design).
The 3D-printed mold should cost less than $1,000 for a simple version. That’s 1% of the cost of a machined mold.
If you want to change the mold, then you can just 3D print a revised version. You can go through dozens of iterations, and you’ll still be saving money.
The turnaround time is also astronomically faster. Instead of months, you’re looking at days.
Saving time and money are the top ways that 3d printing can increase efficiency for injection molders. In this case, you would be printing the actual tooling used in the injection molding machine.
Conclusion
The bottom line is that 3D printing and injection molding should be used together. By 3D printing prototypes and working with those prototypes, you can avoid headaches, save time, and keep your money as you head into the full-scale production phase. If you 3D print the actual mold used in the injection molder, you’ll save even more.
Need help getting started? Our expert drafters at CAD/CAM Services can take care of the 3D modeling for you. We’ll iterate your part during the prototype phase and ensure you’re ready for full-scale production. Get a free quote today to get started.
Recent Posts
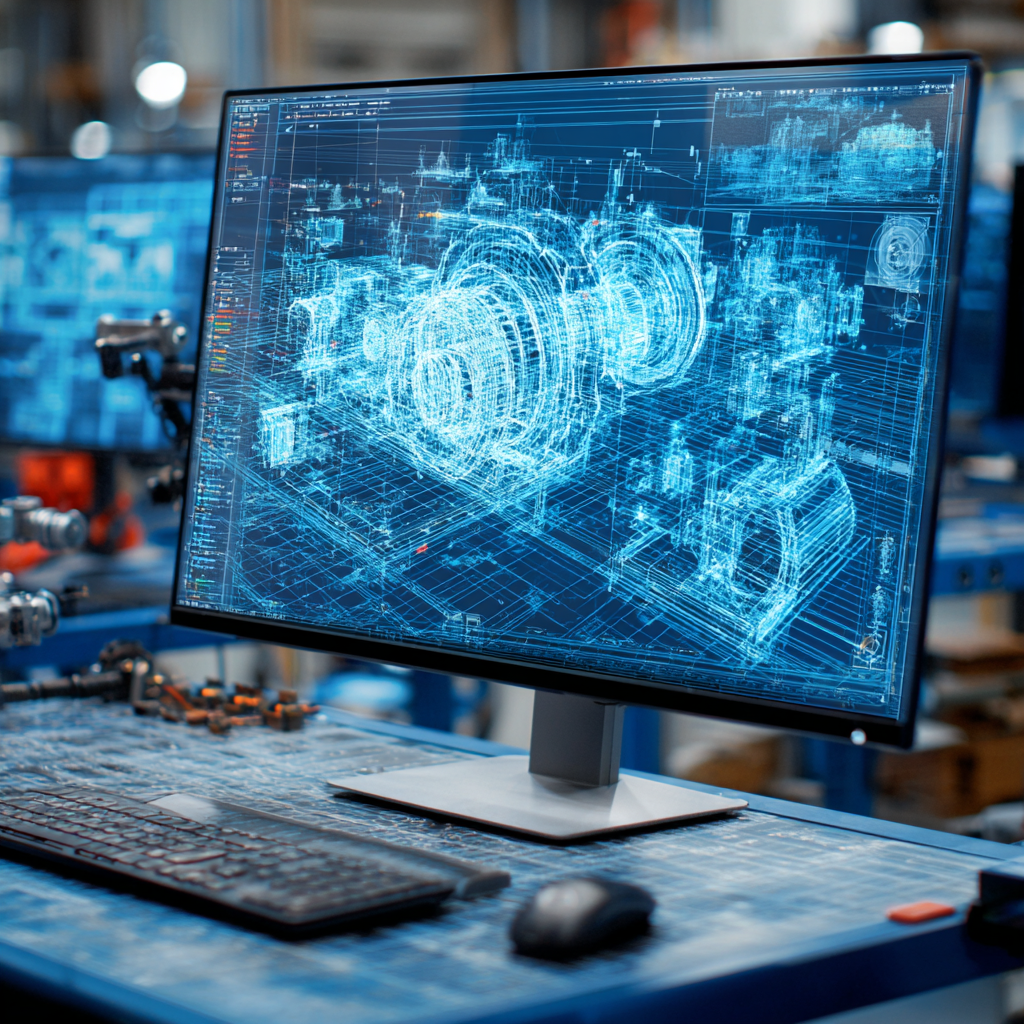
Tips for Picking the Perfect 3D CAD Viewer for Your Needs
This guide will teach you about 3D CAD viewers and outline considerations to make before picking the right one. We review 5 options and pick a clear winner.
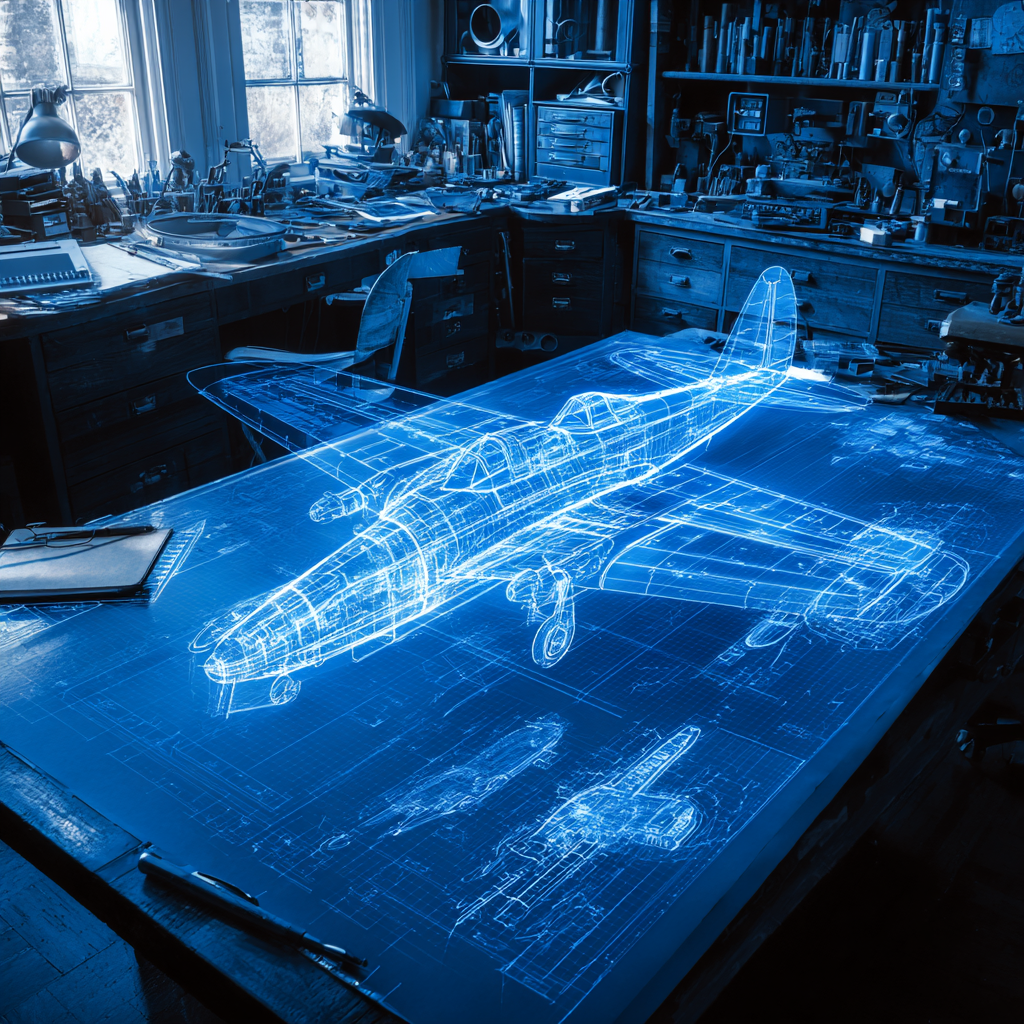
In this guide, you’ll learn how CAD/CAM Services can save you time and money during each digitization project. Digitization can make manufacturing faster than ever before.
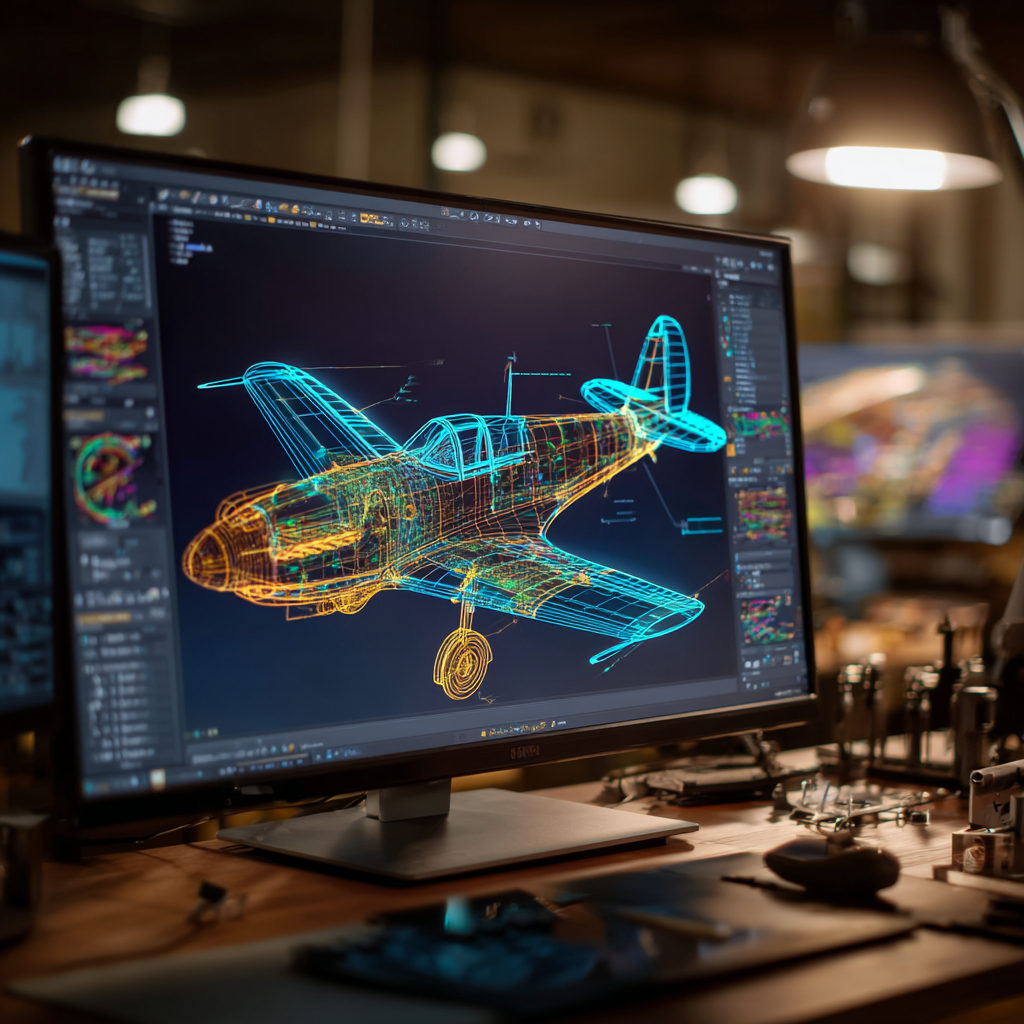
How to Build an Aircraft Model by Converting 3D-Scanned STL Files into Functional 3D STEP Files
This in-depth guide will teach engineers how to use 3D-scanned aircraft files and transform them into manufacturable 3D STEP files with fewer mistakes.