Sheet Metal Design Tips
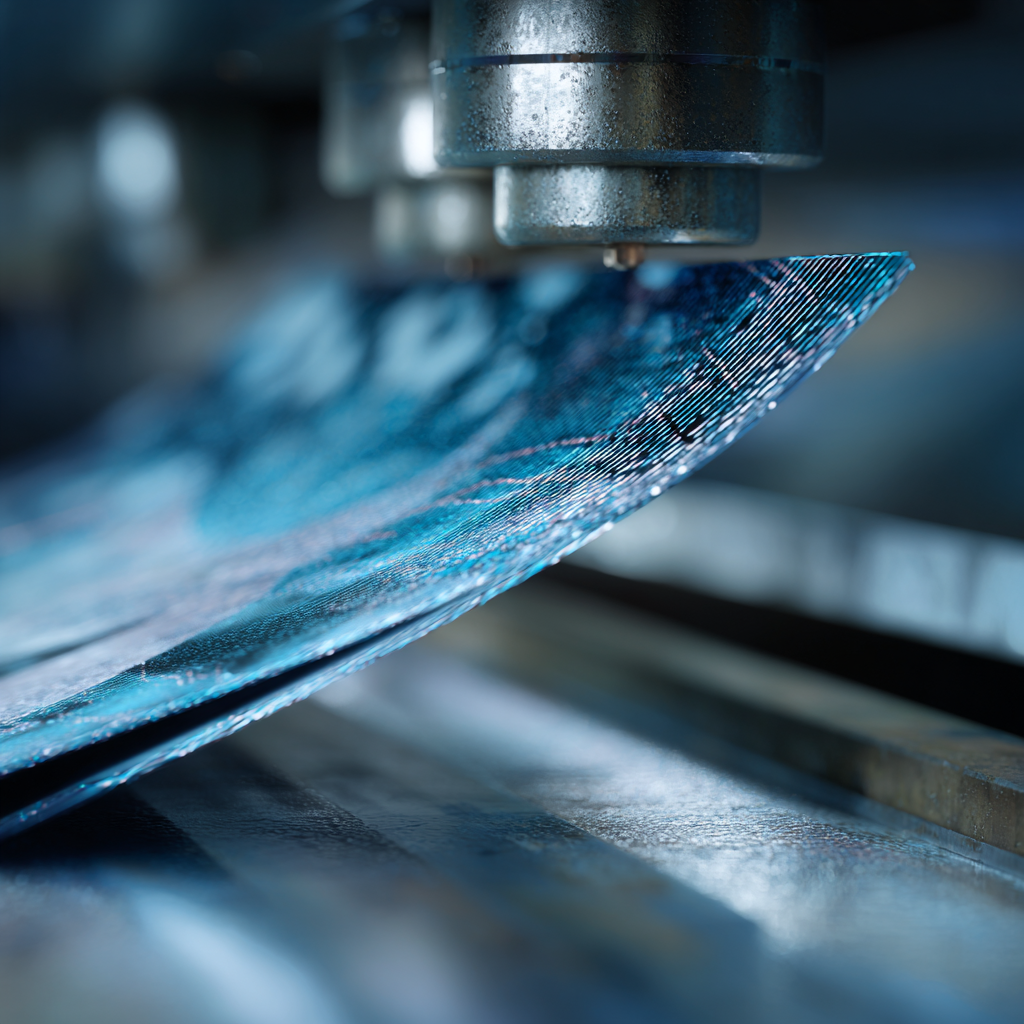
Sheet metal is used for projects across industries and applications. You might use sheet metal on your upcoming automotive design, aerospace upgrade, HVAC project, or as part of your industrial machinery design. Regardless of your application, there are a lot of ways that a sheet metal design can go wrong.
In this guide, you’ll learn 8 tips for better sheet metal designs. These tips will help you save time and money on each fabrication project.
#1: Use Standard Material Thicknesses/ Gauges
The biggest issue we see is designers that use non-standard material thickness in their design. If you’re not using a standard sheet metal gauge, you’re asking a machinist to machine off a thin layer of stock material before they start cutting and assembling the part.
In some cases, this is impossible. In other cases, it will multiply your manufacturing costs and lead times.
Also, remember that different materials have different material thicknesses for the same gauge number. For instance, 10-gauge aluminum, stainless steel, mild steel, and galvanized steel sheets are four different measurements, ranging from 0.1019” to 0.1406” (which can be a massive difference).
Look up a sheet metal gauge chart before starting your 3D CAD design.
#2: Be Careful with Bend Radii
A bend radius is contingent on the material type, thickness, and available sheet metal equipment that your manufacturer is using. It’s really hard to hit a specific bend radius unless you have very high-tech bending equipment, so we typically use “minimum bend radius” on all of our sheet metal parts.
For this tip, think about the bend radius you’re using in your designs. If you’re using the sheet metal functions on a major CAD program like SolidWorks, make sure you click the right boxes to ensure the sheet metal gauge thickness is driving the bend radius you apply to each flange.
#3: Avoid Tight Tolerances
Sheet metal forming has inherently looser tolerances than precision CNC machining. Although plasma cutters and laser cutters can be very precise, it’s hard to maintain overall dimensions and things get even tricker when you have bends.
If you’re using tolerances of a few thousandths of an inch (thou), then you could be driving up the machining costs unnecessarily.
Our suggestion is to always avoid tight tolerances unless you absolutely need them.
#4: Keep the Design Simple
Another general bit of advice that we give to designers and engineers is to keep each design as simple as possible. This is especially true with sheet metal parts and assemblies.
An overly complicated sheet metal assembly will take way longer and cost much more money. In extreme cases, the assembly could be so complex that it would be hard to find a machine shop to handle the project.
#5: Watch the Spacing on Holes and Features
If holes and features are too close together on a piece of sheet metal, you risk the potential for the thin material to tear or create distortions.
Our rule of thumb is to keep slots and holes at least 1.5x the material thickness away from bends and edges. When a piece of sheet metal is bent, the faces are stretched near the corner and you can get an oblong hole that no longer has the clearance for a bolt to go through.
If you are using 0.060” sheet metal, make sure the holes are at least 0.090” away from the bend line. This will ensure your industrial engineering design can be fabricated without any issues.
#6: Think About the Assembly
Assembling sheet metal parts can be trickier than machined parts. For starters, you can’t thread directly into sheet metal and use bolts to assemble the pieces together, so you’ll need to start incorporating different bolts and nuts to assemble the part.
It’s also more difficult to weld sheet metal, and thin sheet metal deforms a lot more than machined parts.
To put it simply, think about how the parts are going to assemble together. You can make things easier by adding self-locating tabs and slots, and you can use a variety of simple fasteners to streamline the assembly.
#7: Try to Use PEM Hardware
PEM hardware is specific to sheet metal, and it’s a form of fastener that is pressed into the sheet metal almost like a rivet. You can find PEM studs, PEM nuts, and other hardware that gets captivated to the sheet metal.
Using PEM hardware can make assembly easier and can avoid welding, which is one of our advanced sheet metal design tips.
#8: Be Careful with Welding
Speaking of welding, another tip for better sheet metal designs is to be careful with the amount of welding used on your parts. Welding thin sheet metal can distort the sheet and ruin the dimensional precision of your parts. Welding together two different pieces of sheet metal can create a warpage due to the uneven heating of the parts.
Knowing how and when to weld together sheet metal parts is a learned skill, and you can always reach out to a local machine shop and ask them fabrication questions (if they’re willing and able to help out, of course).
Conclusion
With these 8 tips, you can start saving time and money on your sheet metal fabrication projects. A little extra time in CAD can save even more time in the machine shop. If the design still seems overwhelming or you need help, reach out to CAD/CAM Services.
We are a full-service outsourced engineering team that can handle some or all of your CAD needs. Our team of almost 100 engineers and designers can create sheet metal designs for you that will minimize your costs and streamline the turnaround time of each manufacturing project. Get a free quote today.
Recent Posts
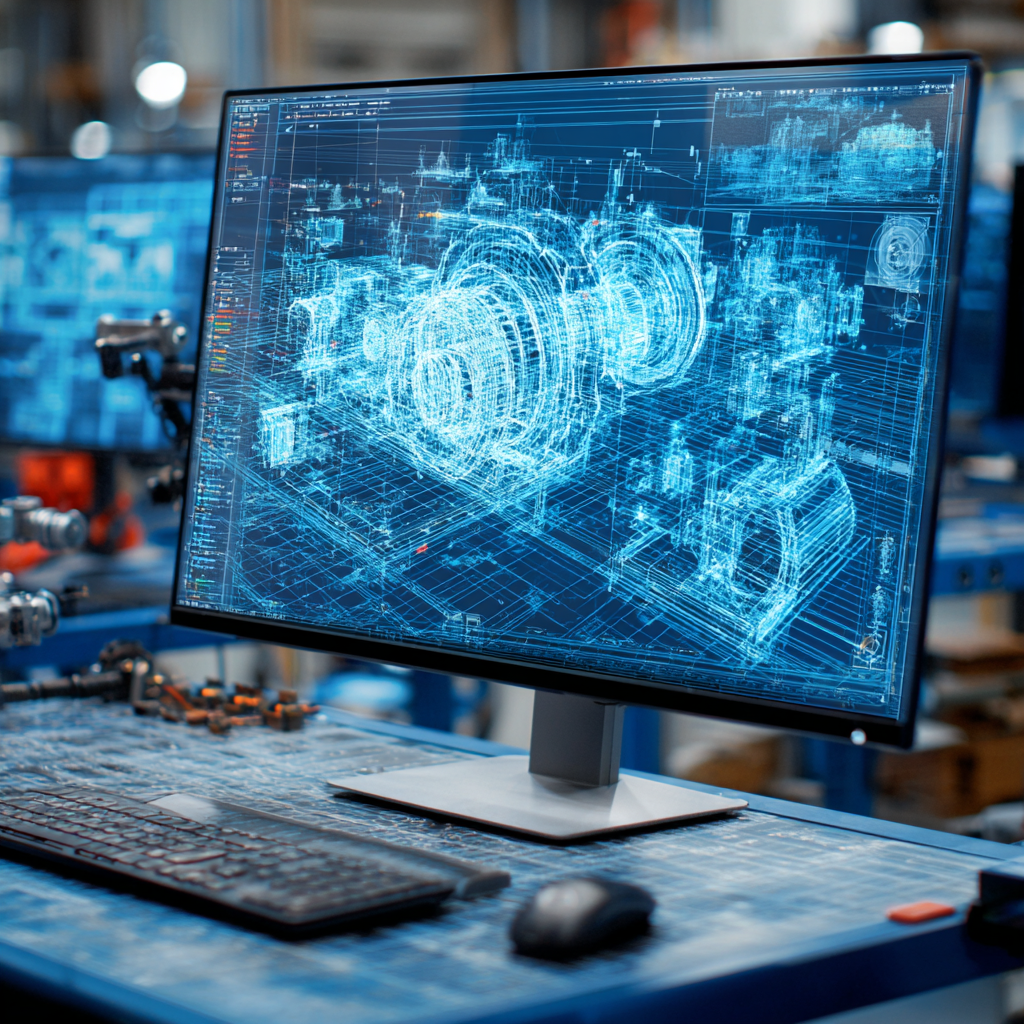
Tips for Picking the Perfect 3D CAD Viewer for Your Needs
This guide will teach you about 3D CAD viewers and outline considerations to make before picking the right one. We review 5 options and pick a clear winner.
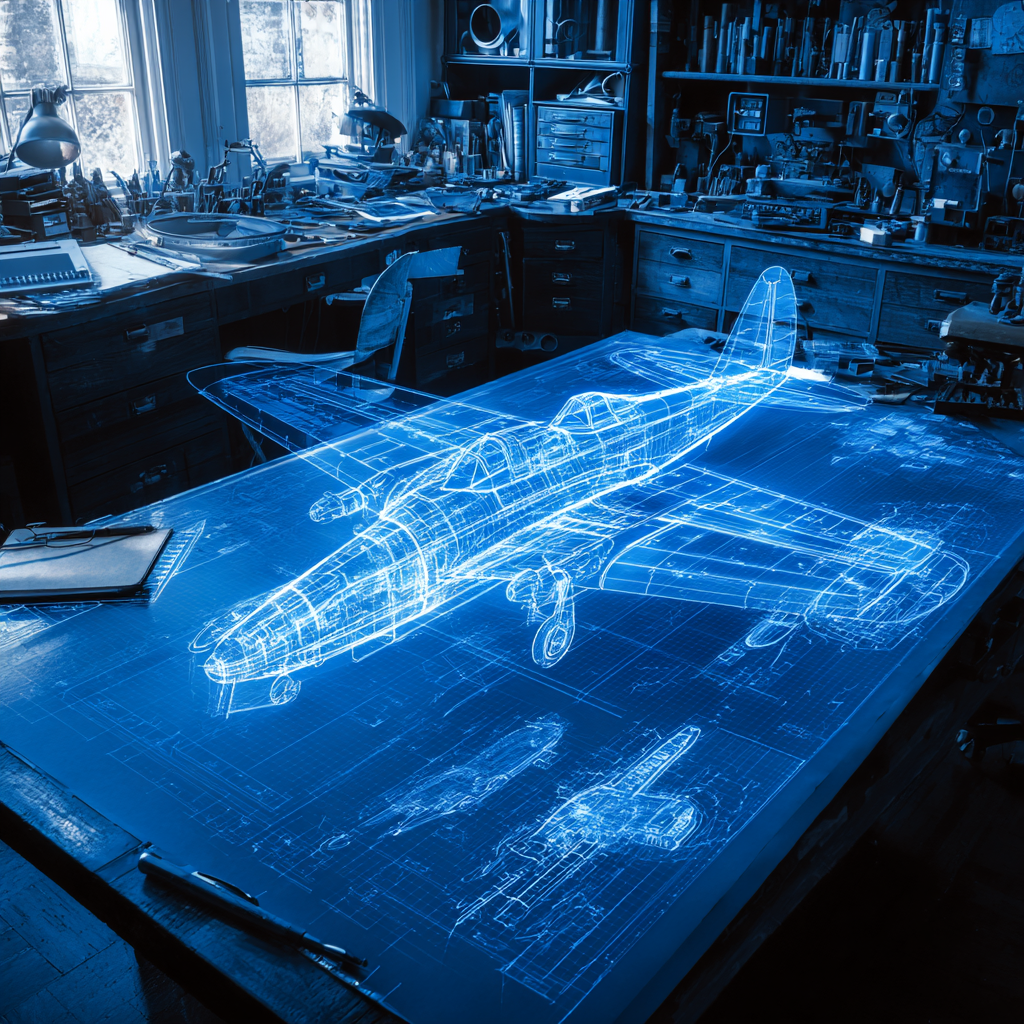
In this guide, you’ll learn how CAD/CAM Services can save you time and money during each digitization project. Digitization can make manufacturing faster than ever before.
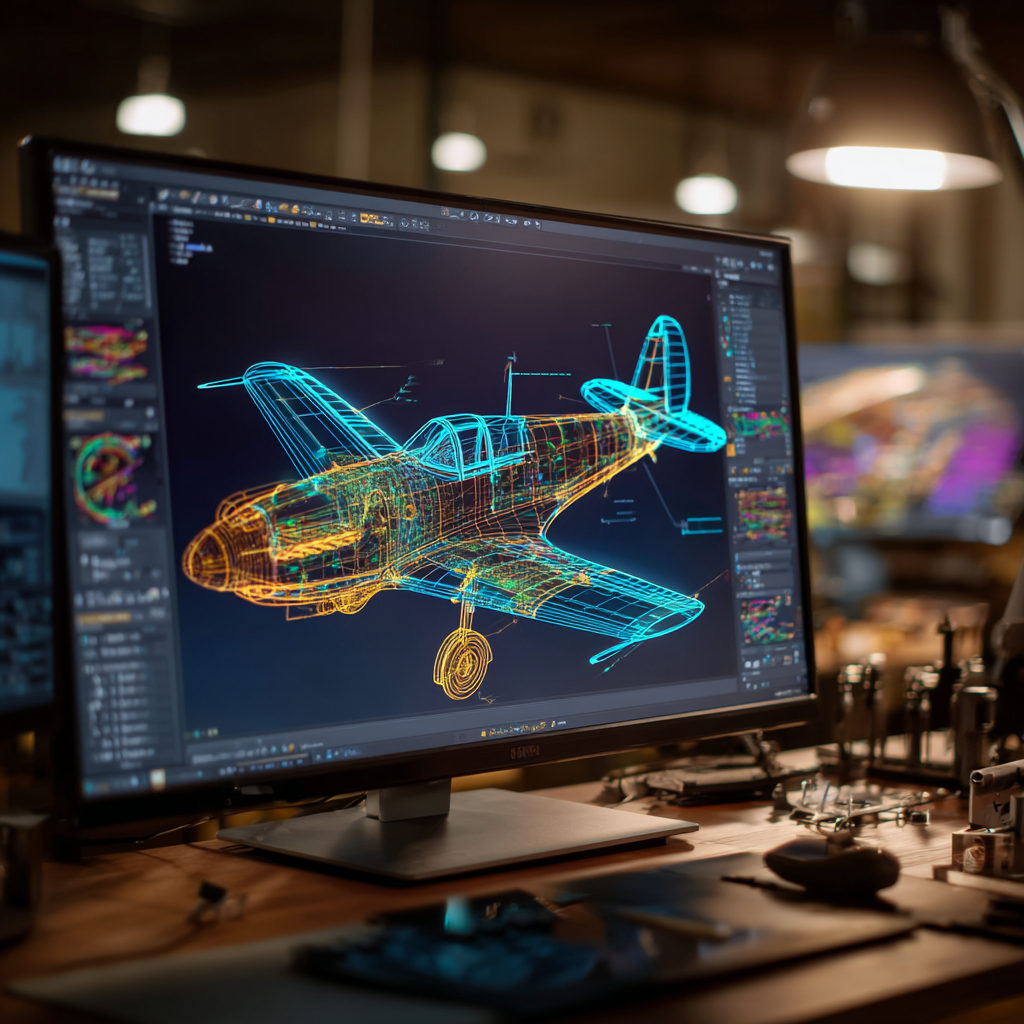
How to Build an Aircraft Model by Converting 3D-Scanned STL Files into Functional 3D STEP Files
This in-depth guide will teach engineers how to use 3D-scanned aircraft files and transform them into manufacturable 3D STEP files with fewer mistakes.